Should You Start with Automotive PCB or Enclosure Design First?
- Posted On:
- October 17, 2024
- Category:
- Ecad
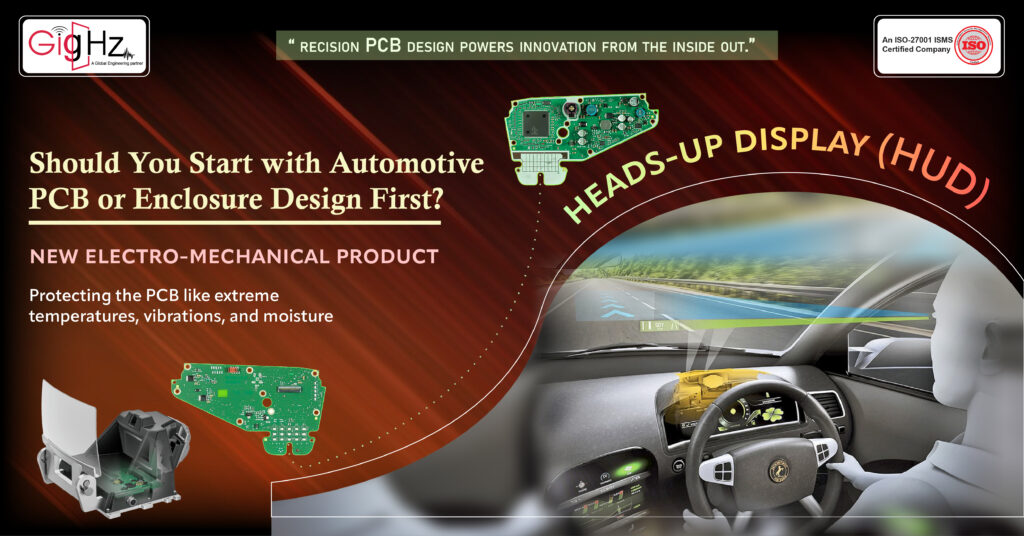
PCB Enclosure Design
When designing a new electro-mechanical product, two critical elements are PCB (Printed Circuit Board) design and enclosure design.
Each plays a vital role in the product’s overall functionality and success, but determining which to prioritize can be challenging.
 Both are essential to the product’s functionality and success, but choosing which to prioritize can be a complex decision.
PCB design is vital because it handles all the electrical connections and power needed for your car’s electronics, like engine controls and entertainment systems.
A well-designed PCB ensures these systems work reliably.
On the other hand, enclosure design is important for protecting the PCB and other parts from things like extreme temperatures, vibrations, and moisture, which are common in cars.
Automotive products often have very limited space.
Starting with PCB design helps make sure that all the electronics fit and work properly.
Starting with the enclosure design ensures that the PCB and other components are housed safely and fit well within the car’s design.
Getting the design order right can affect how much you spend and how long it takes to build your product.
If you don’t get it right, you might face extra costs or delays.
We’ll help you understand how to decide which to focus on first so you can create a product that works well and is protected in tough automotive conditions.
5-Step Guide to Making Smart PCB or Enclosure Design Decisions
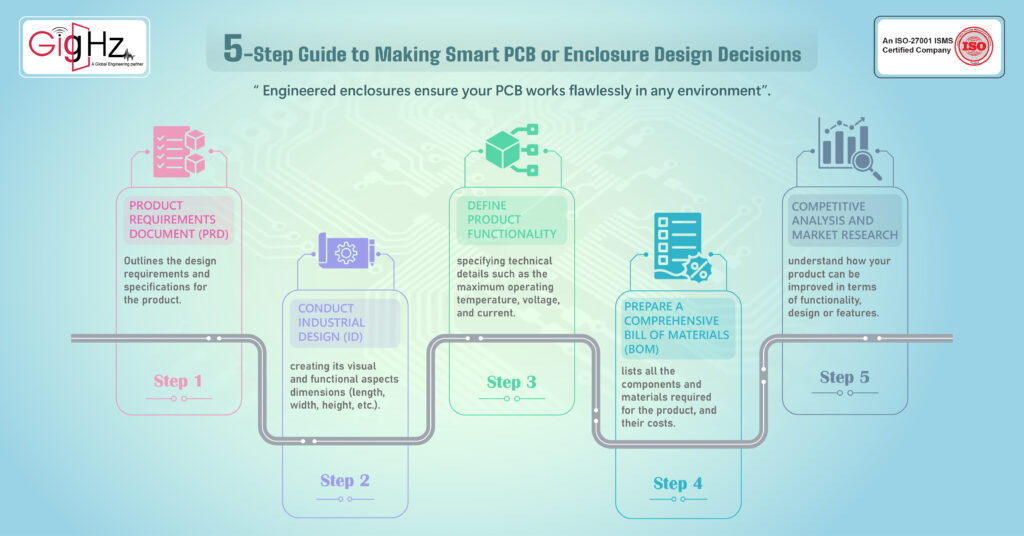
To ensure you make effective design choices for your project, follow these five key steps. Discuss and identify these elements with your team to simplify your decision-making process:
1. Develop a Detailed Product Requirements Document (PRD)
Start by creating a Product Requirements Document (PRD). This document, usually provided by the product engineering team, outlines the design requirements and specifications for the product. It includes details on the product’s form, fit, and function, as well as any specific criteria like durability requirements. The PRD helps the design team understand what features and specifications the product must include.
2. Conduct Industrial Design (ID)
Industrial Design (ID) is essential for the product’s success and involves creating its visual and functional aspects. This step should include detailed or approximate dimensions (length, width, height, etc.), which will help the team design the PCB and place components like buttons and screens accurately.
3. Define Product Functionality
Clearly outline the product’s functionality. This includes specifying technical details such as the maximum operating temperature, voltage, and current. It also describes how the product should perform.
4. Prepare a Comprehensive Bill of Materials (BOM)
Create a Bill of Materials (BOM) that lists all the components and materials required for the product. The BOM should detail where to source these items, the quantities needed, and their costs. This information helps ensure that the project stays within budget and that the design team knows what parts are necessary for the build.
5. Perform Competitive Analysis and Market Research
Analyze similar products on the market and gather samples if possible. This helps you understand how your product can be improved in terms of functionality, design, or features. Additionally, get feedback from potential customers to learn what they value most.
Should You Start with Automotive Electronics PCB or Enclosure Design First?
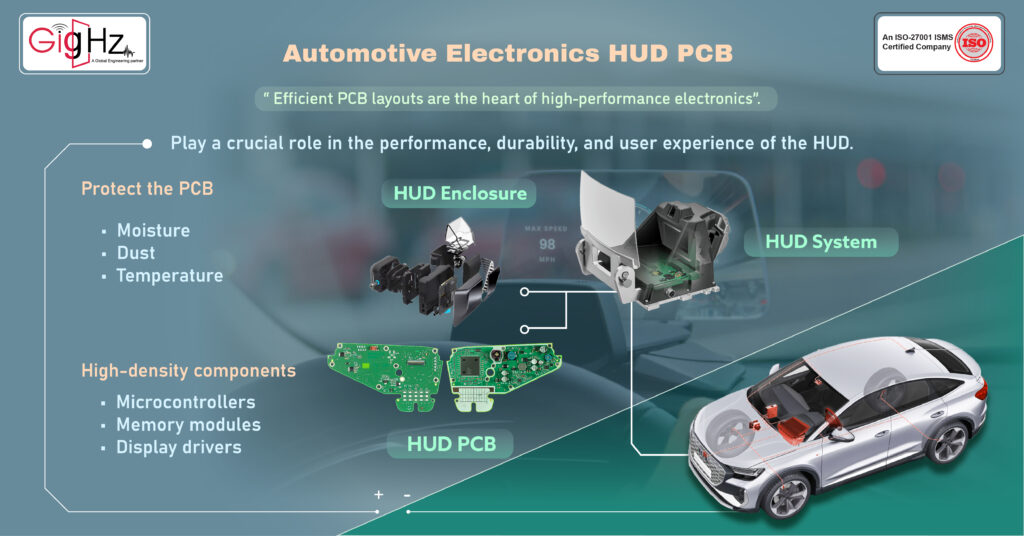
When designing a heads-up display (HUD) system for automotive applications, choosing whether to start with the PCB (Printed Circuit Board) or the enclosure design can be pivotal.
Both elements play a crucial role in the performance, durability, and user experience of the HUD.
A heads-up display is an advanced feature in modern vehicles that projects critical information onto the windshield or a dedicated screen within the driver’s line of sight.
This information typically includes speed, navigation data, and alerts.
Designing the PCB for the HUD System
The design of a HUD involves integrating sophisticated electronics and optics within a compact and robust enclosure to ensure clear visibility and reliable performance under various driving conditions.
- The PCB must accommodate various high-density components, including microcontrollers, memory modules, and display drivers. Proper component placement is essential to ensure signal integrity and reduce electromagnetic interference (EMI).
- The PCB must accommodate various high-density components, including microcontrollers, memory modules, and display drivers. Proper component placement is essential to ensure signal integrity and reduce electromagnetic interference (EMI).
- Given the HUD’s operation in diverse temperature conditions, the PCB design must incorporate effective thermal management solutions such as heat sinks or thermal vias to dissipate heat away from critical components.
- Careful routing of high-speed signal traces is crucial to maintain signal integrity and minimize cross-talk. Using impedance-controlled traces and differential pairs can help achieve stable performance.
- The PCB design must include robust power distribution networks to ensure consistent power supply to all components. This involves designing adequate power and ground planes to handle high current loads and reduce voltage drops.
Designing the Enclosure for the HUD System
The enclosure must be robust enough to withstand vibrations, impacts, and temperature fluctuations typical in automotive environments. High-quality materials such as reinforced plastics or metals are often used.
The design should include features to protect the PCB and other internal components from moisture, dust, and temperature extremes. This can involve gaskets, seals, and protective coatings.
The enclosure design must ensure precise alignment and secure mounting of the HUD system within the vehicle. This involves designing mounting brackets and alignment guides to facilitate proper installation.
The design should account for user interaction, ensuring that the HUD provides clear and unobstructed information. This includes optimizing the display angle and ensuring the enclosure does not cause reflections or distortions.
Cooling and Ventilation
- Heat Dissipation: Proper ventilation and cooling mechanisms are essential to prevent overheating of the electronics. The enclosure design may incorporate vents, fans, or thermal channels to manage heat effectively.
Deciding Which to Prioritize: PCB or Enclosure?
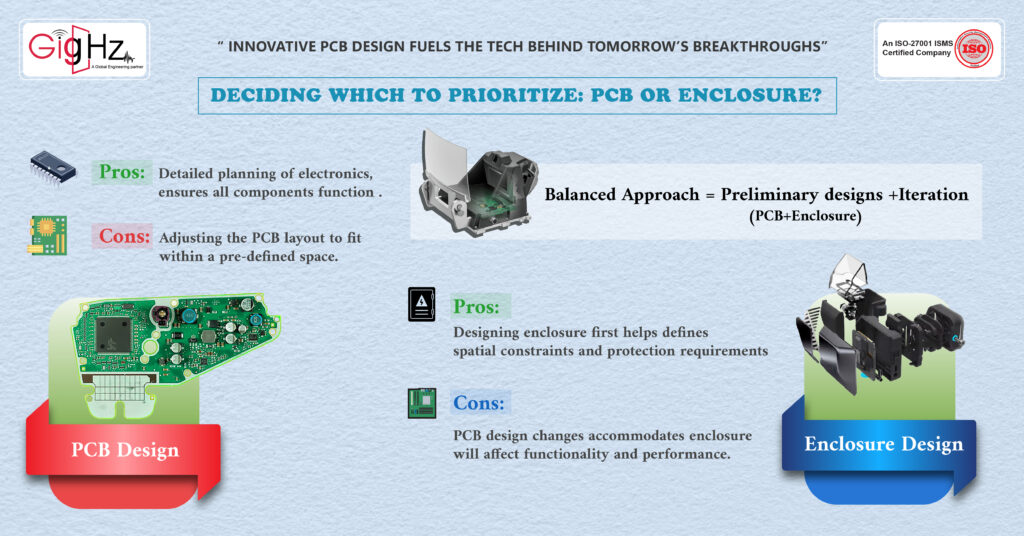
Starting with PCB Design
Pros
Starting with PCB design allows for detailed planning of electronics, ensuring all components function as intended and are properly integrated.
Addressing PCB design first helps identify potential issues with signal integrity, power distribution, and thermal management early in the process.
Cons:
Designing the enclosure later may require adjustments to the PCB layout to fit within a pre-defined space, potentially leading to design challenges.
Starting with Enclosure Design
Pros
Designing the enclosure first helps define the spatial constraints and protection requirements for the PCB. This can guide the PCB design to ensure it fits well and is adequately protected.
Early focus on the enclosure ensures that the HUD system integrates seamlessly into the vehicle’s interior, optimizing user interaction and visibility.
Cons:
Changes to the PCB design may be needed later to accommodate the finalized enclosure, which can affect functionality and performance.
A Balanced Approach
In many cases, a balanced approach is most effective. Begin with preliminary designs for both the PCB and the enclosure and iterate on them together. This iterative process allows for adjustments based on the needs of both components, helping to address potential issues early and ensure that the final product meets all performance and integration requirements.
Final Thoughts
The pcb enclosure design plays a crucial role in the overall performance and reliability of electronic devices. The selection of the right enclosure type is essential, as it impacts the form factor, mechanical protection, and compliance with industry standards. When considering material selection, options such as sheet metal or injection molded plastics provide various benefits, including corrosion resistance and chemical resistance for outdoor or marine environments. A well-designed customized enclosure can significantly enhance the performance of the electronics while allowing for customization to match specific style and branding needs, such as incorporating a logo.
Moreover, the design process should incorporate best practices for airflow and flex considerations, ensuring optimal thermal management for electronic components. Utilizing 3D printing technology can offer innovative solutions in product development, enabling rapid prototyping and adjustments to the design of the enclosure. The right enclosures can be designed to support modular systems while providing essential important functions such as connectivity through connectors.
Discover our Specialities. Visit our Services Page. https://gighz.net/services/
Latest Post
Get Customized Engineering CAD Design Service
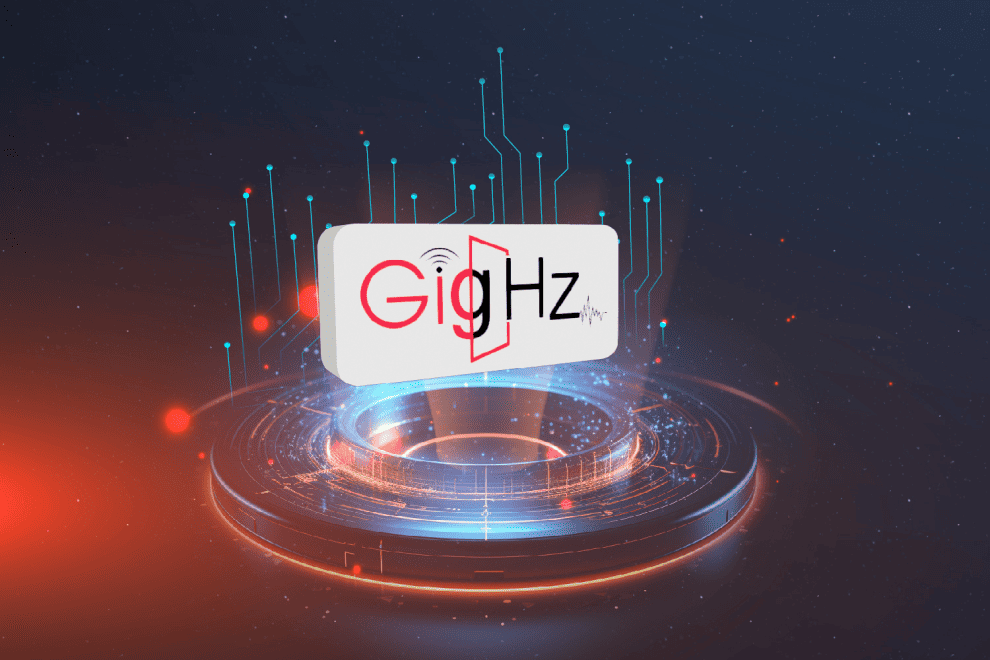
Book a Free Consultation Call​
Partner with Gighz and bring your most innovative design concepts to life. Our engineering cad services accelerate development so you can focus on your big vision.