Why Staying Updated on PCB Component Trends is Essential for Automotive PCB Design?
- Posted On:
- September 3, 2024
- Category:
- Ecad
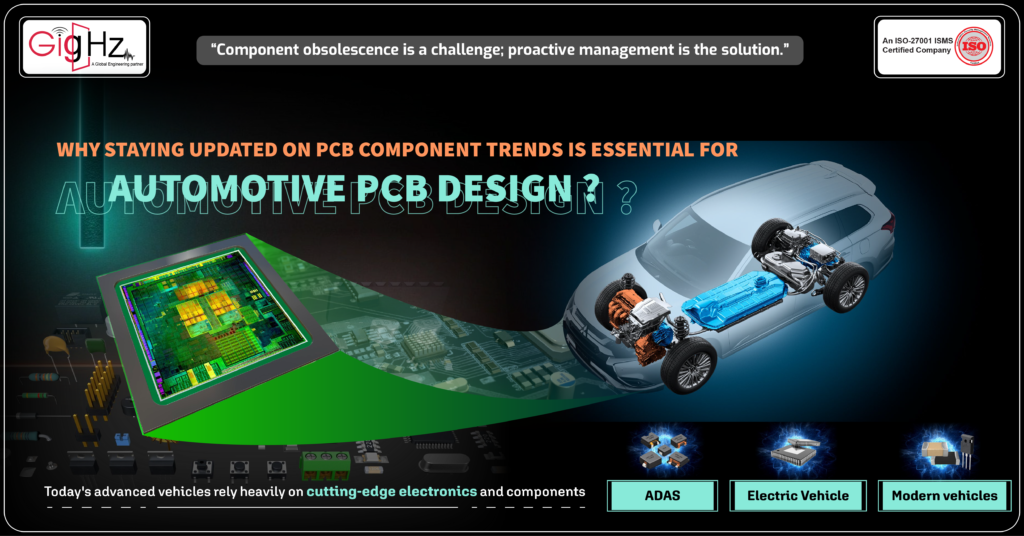
Automotive PCB Design
Imagine a world without cars.
Without them, getting around would be slow and cumbersome.
Public transport would be overcrowded, and personal mobility would be limited. Cars make travel easier, help businesses move goods quickly, and offer us freedom to explore.
Now, think about why our cars are so advanced today. It’s all thanks to the high-tech electronics and components inside them. These parts are what make modern features possible, like safety systems, electric powertrains, and smart in-car technology.
If we didn’t have these advanced components, our cars wouldn’t be as safe, efficient, or smart. For automotive PCB designers, it’s crucial to stay up-to-date with the latest trends in component technology.
Why?
Because the parts we use in car designs need to handle new challenges and technologies.
For example, as cars become more electric and self-driving, they need components that can manage higher power levels and process data quickly. Keeping track of the newest components means you can design PCBs that meet these demands and keep up with the latest technology.
Today’s advanced vehicles rely heavily on cutting-edge electronics and components. These parts are responsible for key features such as advanced driver assistance systems (ADAS), electric powertrains, and in-car connectivity. Without these technologies, our cars wouldn’t be as safe, efficient, or smart.
PCB Component Trends: Are They Key or Are They Keys?
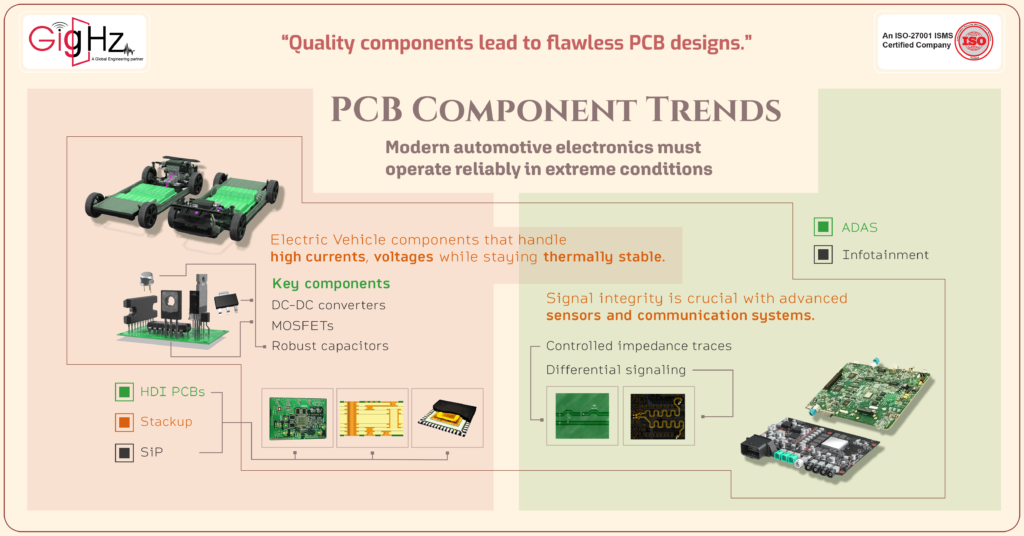
Modern vehicles, especially electric ones, need components that handle high currents and voltages while staying thermally stable. Key components include MOSFETs with low RDS (on) for reduced power losses, high-efficiency DC-DC converters, and robust capacitors. Effective integration requires knowledge of power distribution networks (PDNs) and careful thermal management directly impacting signal integrity.
Maintaining signal integrity is crucial with advanced sensors and communication systems. Controlled impedance traces, differential signaling, and components with high common-mode rejection ratios (CMRR) ensure minimal signal degradation in ADAS, infotainment, and communication modules. Improved signal integrity allows for more compact and feature-rich designs.
As cars become more compact and feature-rich, components are designed to be smaller yet more powerful. HDI (High-Density Interconnect) PCBs with Microvias, fine pitch components, and multi-layer stackup maximize routing density. System-in-Package (SiP) technology combines multiple ICs into a single package, reducing space while enhancing performance.
Modern automotive electronics must operate reliably in extreme conditions. Components are tested for durability and safety to ensure performance in various temperatures and under mechanical stress. Robust design practices like conformal coating, potting, and stringent EMI/EMC testing ensure long-term reliability. Adhering to ISO 26262 for functional safety and AEC-Q100 for automotive-grade components guarantees system safety and reliability.
So what components are printed circuit boards made of?
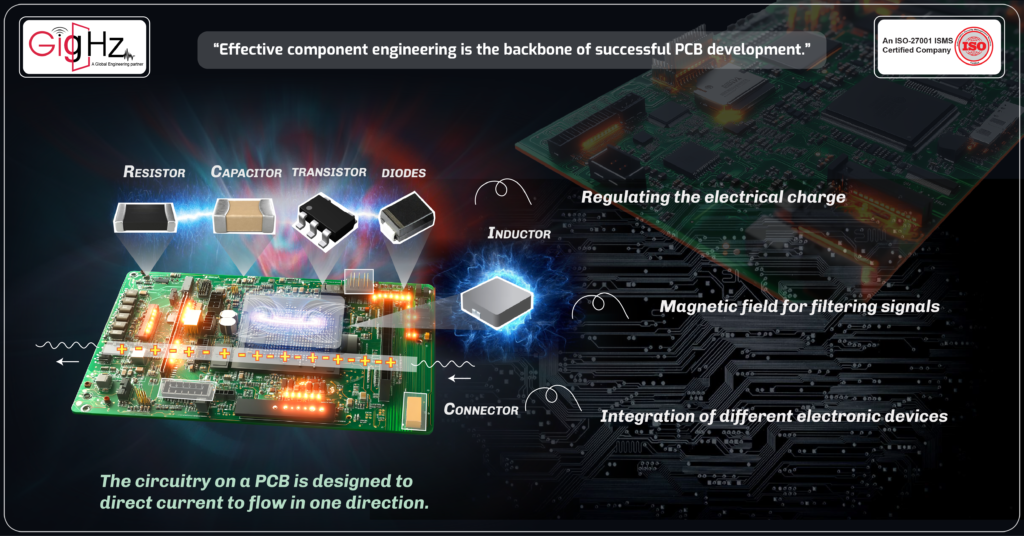
Printed circuit boards (PCBs) are essential components in the world of electronic design and manufacturing. The components that make up a PCB include resistors, transistors, diodes, inductors, and various other electronic components.
A PCB is a common platform used to connect these components in a circuit design, allowing for the flow of electrical energy and the dissipation of heat.
The circuitry on a PCB is designed to direct current to flow in one direction, with components like resistors and capacitors playing key roles in regulating the voltage and current levels in an electronic system.
Suppliers use techniques and tools to optimize the manufacturability of PCBs and enhance the design performance of electronic products.
The materials used in the construction of a PCB are carefully selected to ensure the insulation and resistance value meets the requirements of the design.
Components like resistors, transistors, and diodes are placed on the PCB to perform specific functions, such as regulating the electrical charge or storing energy. Inductors are used to create a magnetic field for filtering signals, while connectors allow for the easy integration of different electronic devices. During the assembly process, solder is used to melt and secure components in place, ensuring the functionality of the device. By using techniques and methods like CAD and BOM, manufacturers can optimize the cost and performance of PCBs for various applications.
Why Staying Updated on PCB Component Trends is Essential for Automotive PCB Designers?
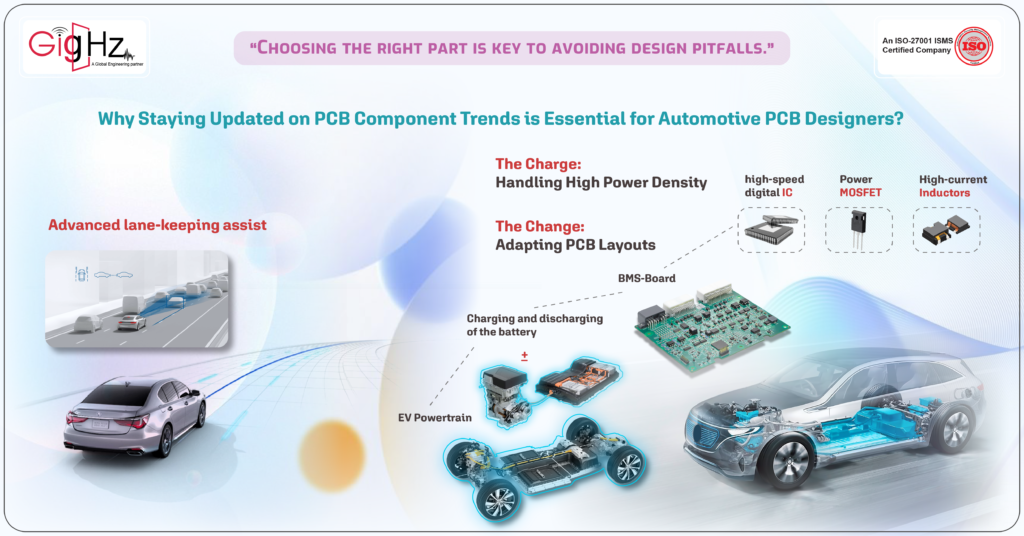
Complexity of Modern Automotive Electronics
Designing a car with advanced lane-keeping assist and a high-definition touchscreen. You have to ensure that data from various sensors—like cameras and radar—flows seamlessly to the central processing unit. At the same time, you need to manage multiple power sources, from the infotainment system to the engine control unit, all while keeping these components cool. Failure to manage high-speed signals, power distribution, and heat effectively can lead to system failures or performance issues.
In this complex environment, you can use advanced components to enhance performance.
For instance, high-speed digital ICs are designed to process vast amounts of sensor data quickly and accurately. To handle the heat generated by these components, you might use specialized heat sinks or thermal vias that efficiently transfer heat away from critical areas. These innovations not only ensure that all systems operate reliably but also help in maintaining the overall efficiency and safety of the vehicle.
Electrification and Hybrids: A ‘Charge’ in Design or a ‘Change’ in Design?
As the automotive industry shifts towards electrification and hybrid vehicles, PCB designers face a significant “charge” and “change” in their work.
The Charge: Handling High Power Density
A high-performance EV where the battery and motor require robust power management. Components like power MOSFETs handle large currents and voltages, while high-current inductors manage energy flow. For example, in the battery management system (BMS), power MOSFETs control the charging and discharging of the battery. High-current inductors smooth out current fluctuations. Thermal interface materials help dissipate heat generated by these components, preventing overheating and ensuring reliable operation.
The Change: Adapting PCB Layouts
High-speed data lines in an EV must maintain signal integrity despite increased electromagnetic interference (EMI) from the powertrain. This means redesigning trace routing to minimize noise and using shielding techniques. Additionally, the compact space in hybrid and electric vehicles demands innovative layout strategies. Designers might employ advanced techniques like multi-layer PCBs and integrated passive components to fit more functionality into smaller spaces without compromising performance.
Final Thoughts
It is evident that pcb design and pcb assembly play a crucial role in the development of electronic devices.
By understanding the intricacies of common pcb technologies and incorporating best practices such as bipolar transistor biasing and insulating sensitive components, engineers and designers can optimize the performance of their designs. Utilizing cadence software for schematic capture and cost optimization can further enhance the design process. Our team of experts is equipped to handle a wide range of pcb components, including semiconductors, inductors, and power supplies, ensuring that your pcb is tailored to meet specific operating conditions.
To know more insights,
Schedule a Call. Book a Free consultation now https://calendly.com/gighz/30min
Table of Contents
Latest Post
Get Customized Engineering CAD Design Service
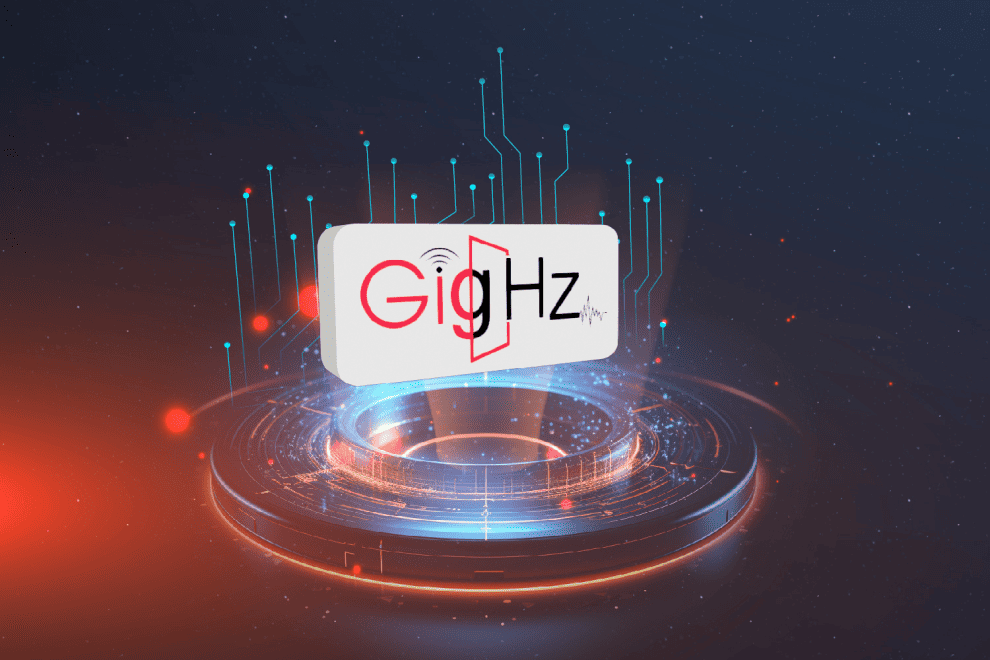
Book a Free Consultation Call​
Partner with Gighz and bring your most innovative design concepts to life. Our engineering cad services accelerate development so you can focus on your big vision.