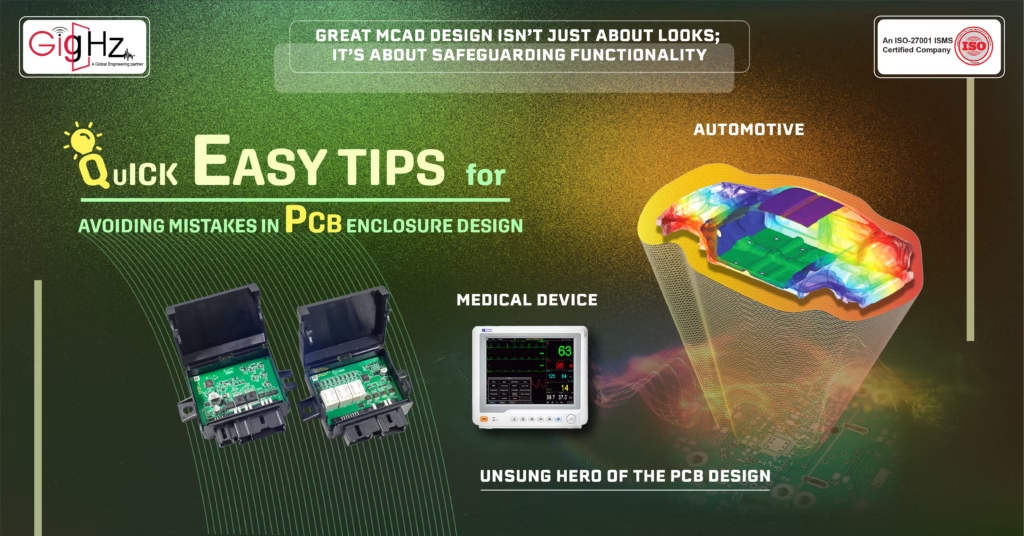
Quick Tips
In the early days of my career,
I focused heavily on circuit layout and component selection, believing that once I had that nailed down, the rest would fall into place.
It seemed like the logical next step:
Perfect the circuit, pick the right components, and the job would be done.
However, I quickly learned that the enclosure—
The unsung hero of the PCB design—was just as important as the components themselves.
Through years of hands-on experience and refining my design process,
I discovered that a poorly designed enclosure can lead to thermal issues, mechanical failures, and electrical interference—
Problems that could easily derail an otherwise perfect PCB.
These issues often don’t become apparent until later in the process, but by then, they can be costly to fix.
As I continued to refine my approach,
I developed a continuous procedural workflow that ensured I was considering the key technical specifications from the very beginning.
Whether I was designing for automotive, medical, or high-speed electronics,
I started incorporating thermal management, mechanical stability, and electrical shielding into my enclosure designs right alongside the PCB layout.
This proactive approach allowed me to avoid the costly pitfalls of poor enclosure design and ultimately ensured that my projects ran more smoothly, with fewer unexpected challenges.
The process I use now is built on years of trial, error, and continuous improvement.
In this post, I’ll share the lessons I’ve learned along the way, along with actionable tips to help you avoid common mistakes and design enclosures that truly complement your PCBs, ensuring they perform optimally in the real world.
Quick Easy Tips for Avoiding Mistakes in PCB Enclosure Design
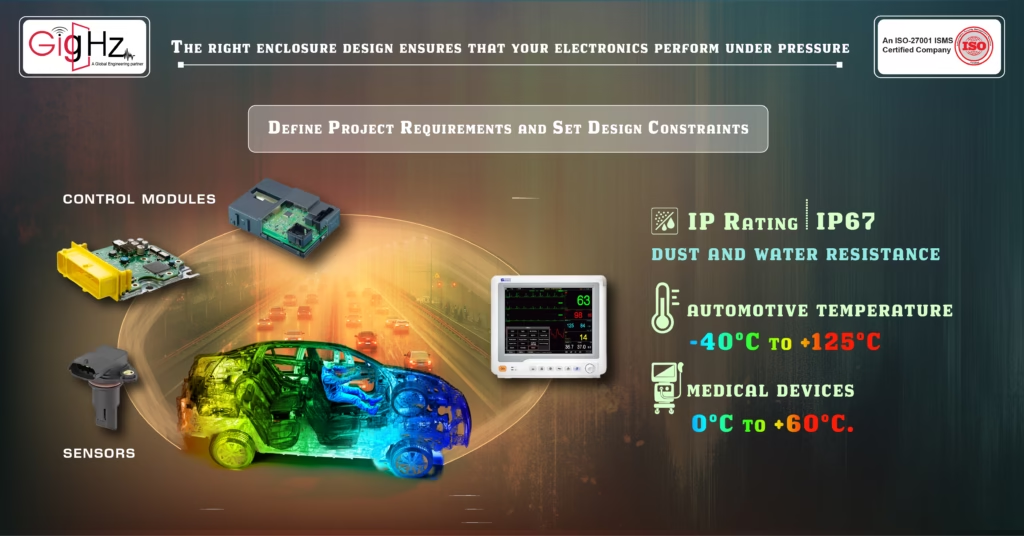
1. Define Project Requirements and Set Design Constraints
In the early stages of any design, clear and specific requirements must be established.
My first step is always to define the project’s specific technical requirements and establish design constraints before moving forward.
For instance, in automotive designs, thermal and size constraints play a crucial role.
The ambient temperature range in automotive environments can reach -40°C to +125°C depending on the location, which means the enclosure must protect the PCB from extreme heat and cold.
Additionally, the size constraints of the enclosure must match the specific geometry of the automotive unit, which could include tight spaces in control modules, sensors, or power systems.
Establishing these specifications upfront ensures that the design meets functional and regulatory needs.
Key Specifications to Consider:
- Thermal Limitations: Operating temperature range for automotive designs should be -40°C to +125°C, while for medical devices, it may range from 0°C to +60°C.
- IP Rating: In automotive or medical devices, you’ll often need an IP67 rating for dust and water resistance.
- EMC Requirements: Standards like ISO 11452 (automotive EMC) must be met, especially in automotive and medical device designs where electromagnetic interference (EMI) can cause operational issues.
2. Prioritize Thermal Management Throughout the Design Process
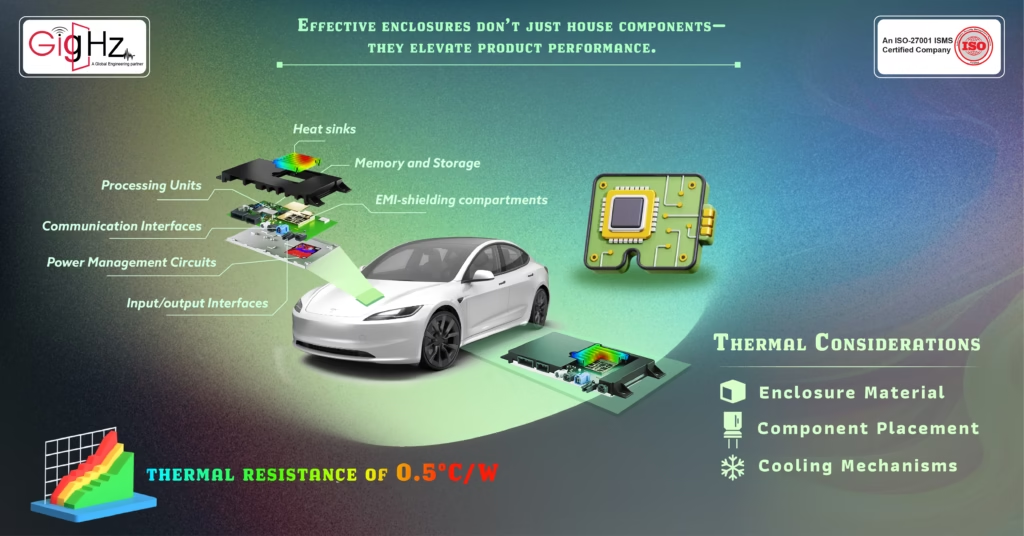
One of the biggest lessons I’ve learned is how crucial thermal management is in PCB enclosure design.
When I first started, I focused more on the electrical routing and less on heat dissipation, leading to overheating issues in finished products.
Now, I include thermal analysis at every stage of the design process.
I consider the thermal resistance of the enclosure material, the use of heat sinks, and the strategic placement of components to reduce heat generation.
In automotive applications, for instance, power transistors, microcontrollers, and sensors generate significant heat, which must be efficiently dissipated to avoid failure.
Thermal Considerations in the Continuous Workflow:
·
Key Factors for Effective Thermal Management in Automotive Enclosures
- Enclosure Material: Selecting materials with the right thermal conductivity is crucial. For example, aluminum enclosures with a thermal conductivity of around 205 W/mK are often used in automotive designs for efficient heat dissipation.
- Component Placement: Position components that generate significant heat, like power transistors, away from sensitive parts. It’s also important to place them near ventilation slots or heat sinks to improve heat dissipation.
- Cooling Mechanisms: In some designs, integrating passive cooling elements such as thermal pads or heat sinks with a thermal resistance of 0.5°C/W or lower can greatly enhance the thermal performance, helping to maintain optimal operating temperatures.
By carefully considering these aspects, we can ensure efficient thermal management that supports the reliability and longevity of the design.
3. Ensure Mechanical Integrity and Robustness
Mechanical integrity is one of the most critical aspects of PCB enclosure design.
Early in my career, I always consider the stresses the enclosure would face in real-world environments.
I learned that robust mechanical design is essential to ensuring the long-term reliability of the product.
For instance, in automotive applications, enclosures are subjected to vibration, shock, and high-pressure environments.
Using materials with sufficient impact resistance and designing with stress relief mechanisms is key.
Materials such as polycarbonate (with an impact resistance of 9 J/m²) or Aluminium (which has high tensile strength) are often preferred for durability and shock absorption.
Key Mechanical Design Factors:
Material Choice: Materials like polycarbonate or ABS (Acrylonitrile Butadiene Styrene) for medical enclosures offer a balance between durability and ease of fabrication.
Gasket and Seals: Proper seals around the enclosure prevent ingress of moisture and dust, especially important for medical and automotive applications requiring IP67 rating.
Mounting and Vibration Dampening: When designing for automotive, it’s important to integrate rubber gaskets or vibration dampeners to protect sensitive components and maintain mechanical integrity.
4. Optimize for EMC Compliance
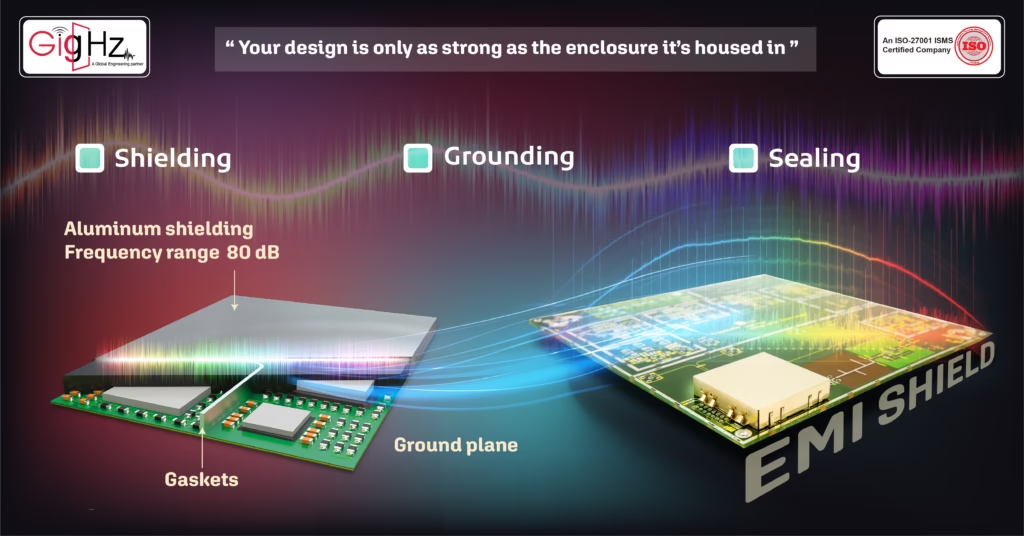
Electromagnetic compatibility (EMC) is one of the most technical and demanding aspects of PCB enclosure design.
In my early designs, I often overlooked the importance of preventing interference between the PCB and external electromagnetic fields, especially in automotive or high-speed applications.
Now, EMC compliance is integrated into the entire design flow.
The choice of materials, grounding techniques, and shielding methods are all tailored to meet specific EMC standards.
EMC Considerations in the Workflow:
· Shielding: Use of metal enclosures made of aluminum or steel, with shielding effectiveness of up to 80 dB or more, depending on the frequency range and application.
· Grounding: Ensuring a proper ground plane design and using via stitching to provide a continuous ground connection throughout the enclosure.
· Sealing: Integrating conductive gaskets for environmental sealing while maintaining an electrically conductive path.
Summary
The blog highlights the significance of electronic enclosure design in the realm of product development for electronic devices.
A well-thought-out enclosure serves to protect sensitive electronic components while enhancing the functionality and performance of the electronics inside.
Key aspects such as pcb design, printed circuit board layouts, and cable management play crucial roles in ensuring that the enclosure design accommodates the necessary connectors and ports.
Designers often utilize sheet metal, plastic parts, or even 3D printing to create prototypes that meet the required size and form factor.
Customization options like cutouts and mounting options can also be integrated into the design to ensure the enclosure protects against environmental factors, while maintaining rigidity and adequate airflow.
Don’t miss out on our upcoming posts — follow us https://www.linkedin.com/in/chandra-thimma/recent-activity/all/ for more actionable insights and design tricks!
Latest Post
Get Customized Engineering CAD Design Service
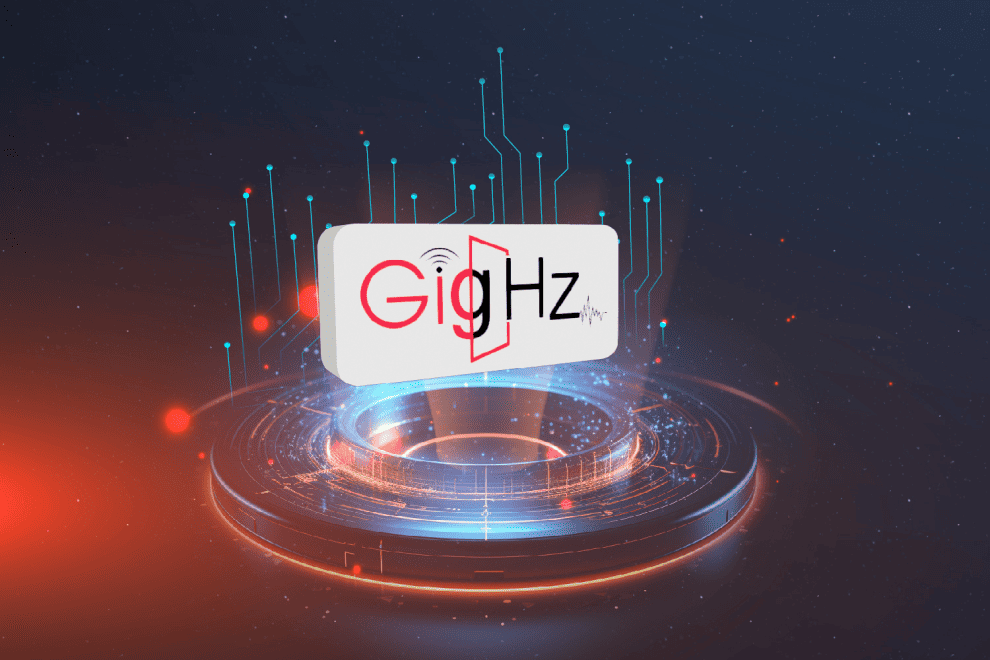
Book a Free Consultation Call​
Partner with Gighz and bring your most innovative design concepts to life. Our engineering cad services accelerate development so you can focus on your big vision.