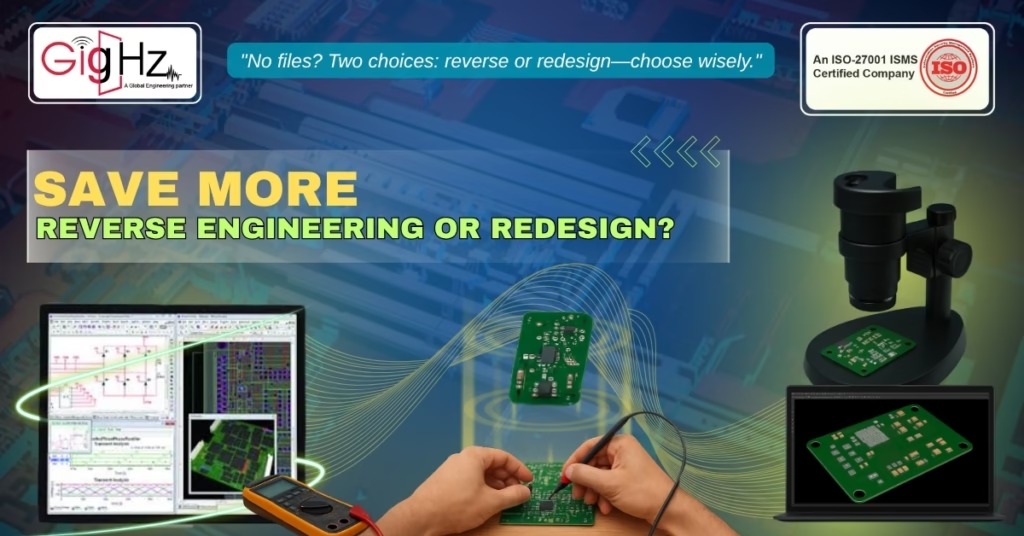
If you are someone managing legacy hardware, then this post isn’t optional but rather very urgent!
It doesn’t matter whether you are trying to extend the life of a product or adapt to changing requirements – You will definitely hit major roadblocks like:
- Outdated documentationÂ
- Missing ModelsÂ
- Or worse – No files at all!
Sounds like a nightmare, right? Yes, when those major engineering design sources vanishes completely, then you are left with just two paths:Â
- Reverse engineer whatever you are left withÂ
- Start from scratch with a full redesign plan.
So, which one is the best way in terms of engineering design services? Also that actually saves time, money and efforts to a great extent.Â
Well, let’s break it down with clear and practical insights.
Reverse Engineering: When the Old Still Works
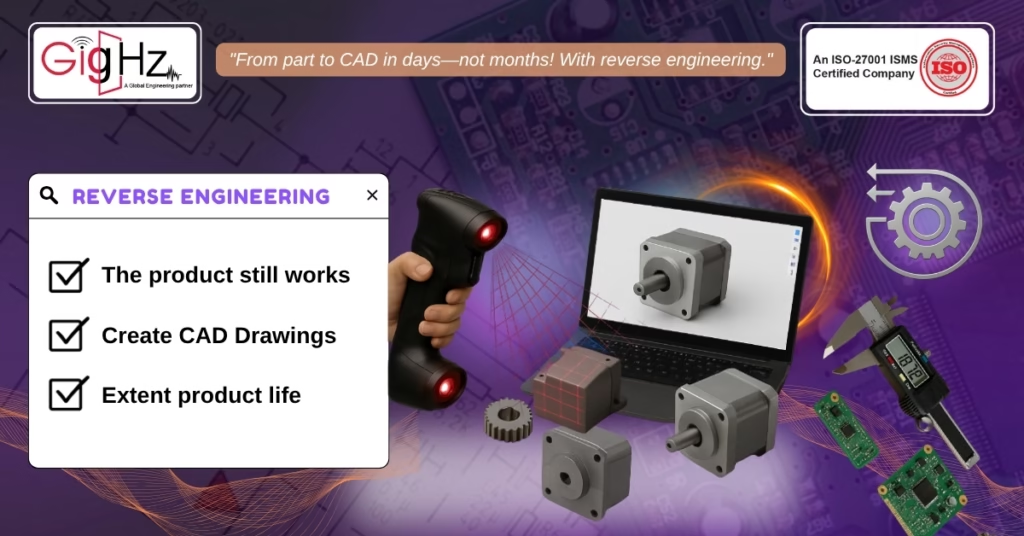
Now, as we all know reverse engineering involves recreating your final product from its original design files. Over here, you work backward—from hardware to a digital model.
Talking of which, Let me explain why many teams choose this route:
- First, the product still works and all you need are updated models.
- Secondly, you may want to create or update accurate mechanical engineering CAD drawings later.
- Third, you may need to extend your product life and not reinvent it.
For instance, in industries like industrial automation or medical equipment – Replacing an entire product line for just one outdated bracket or chassis is a rare option. Likewise, reverse engineering also allows you to stay compliant with engineering drawing & CAD standards while just replicating critical geometry.
How to Perform Reverse Engineering of a Product:
Now, if you are wondering on how exactly the process of reverse engineering works – Then, here’s a simplified breakdown:
- Physical Inspection: Always, start by analyzing the physical product in the first place. Then, understand the components, joints, and assembly placements. Afterwards, take down notes on what’s critical like dimensions, fit, and materials.
- Disassembly (if required): Cautiously, break down the product into parts without damaging them. As, this helps you scan or measure the internal components more accurately.
- Scan the Geometry: Utilize 3D scanners or CMMs to capture accurate shapes and dimensions.
- Data Processing & Clean-Up: Next, clean the scanned data to remove noises. Then, proceed to convert the point cloud into a mesh, & then into surfaces or solids using softwares like Geomagic, SolidWorks, or CATIA.
- Create CAD Models: Now, initiate reconstructing the part in CAD software using the scan data as reference. Likewise, this is where the digital model is made fully editable for engineering or manufacturing.
- Validate & Check Tolerances: Additionally, you must ensure that the model matches the original specs and fit.
- Documentation & Output: Finally, once you validate it! Export the 2D engineering drawings or prepare the file for 3D printing, machining, or analysis.
Moreover, with the right services, you may seamlessly switch from a physical part to a detailed 3D model in just days not months.Â
Redesign: When It’s Better to Start Fresh
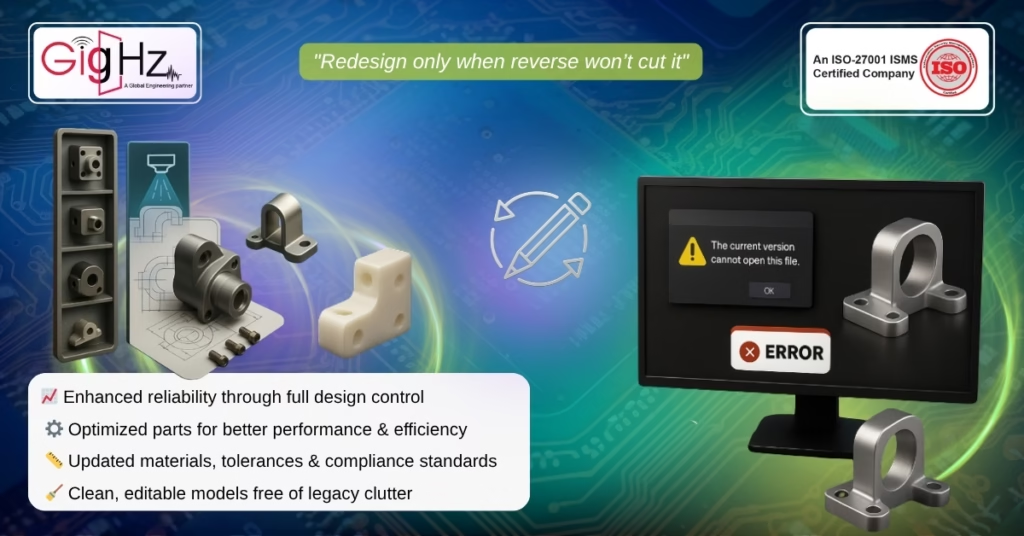
Now, on the flip side, at times redesigning might be the smarter move if the following circumstances occur:
- The existing part is functionally outdated or completely inefficient.
- Then, you are upgrading materials, tolerances, or compliance factors
- Or, the current design doesn’t meet modern mechanical design / CAD program capabilities.
Also, redesigning allows you to modernize things completely like — clean models, optimized parts, and updated performance.
But obviously it’s quite resource-intensive. Overall, it often takes longer completion, involves more testing, and sometimes leads to scope creeps. Unless there’s a compelling reason (like safety, compliance, or cost savings), redesigning might be overkill for sustaining older products.
Which Option Saves More?
Time
- Reverse Engineering: It’s faster only if you have the part and good metrology tools.
- Redesign: Often slower due to concept generation, prototyping, and validation practices.
Cost
- Reverse Engineering: CheaperÂ
- upfront costs, as it allows teams to reuse existing components.
- Redesign: Higher cost, but may lower long-term maintenance cost.
Flexibility
- Reverse Engineering: It’s very limited to what already exists in the first place.
- Redesign: Fully customizable for new performance or integration needs extensively.
Risk
- Reverse Engineering: Minimal change = fewer surprises of course.
- Redesign: Obviously, good opportunity … but, greater room for hidden mistakes.
Action Plan: How to Choose Wisely
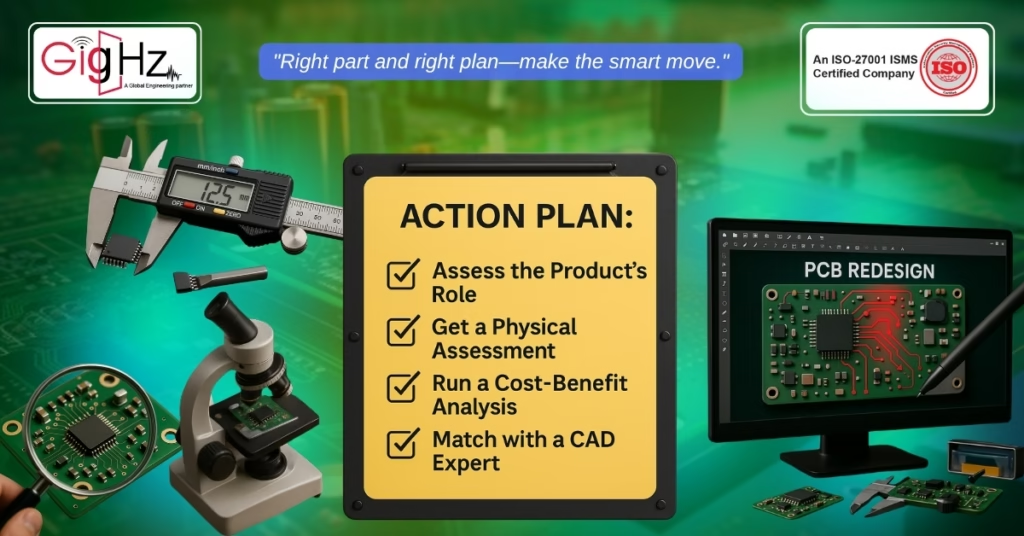
- Assess the Product’s RoleÂ
Claridy, first is it part of a legacy system that needs minimal disruption? Otherwise, reverse it if it’s bottlenecking your workflow or costing you too much. Afterwards, you may consider redesigning it.
- Get a Physical Assessment
Do engage an expert in engineering drawing to inspect the part. As, some geometries are not worth reverse modeling if they can’t be accurately measured or scanned.
- Run a Cost-Benefit Analysis
Then, include not just development costs, but testing, requalification, and potential production downtimes as well.
- Match with a CAD Expert
Lastly, always make sure whoever supervises the project knows engineering drawing & CAD standards in and out! Also, that they use the right mechanical design / CAD program for your industry.
Bottom Line: You Don’t Have to Guess
Summing up, the truth is that neither reverse engineering nor redesign is always a “better” option. Because it depends entirely on your goals, timeline, and product lifecycle.
So, if you are only preserving something that still works, then reverse engineering can keep your project moving without blowing the budget. But if you are innovating or scaling up, then a swift and smart redesign can future-proof your entire line.
Either way, investing in high-quality mechanical engineering CAD drawings is highly essential. As, it bridges the gap between concept and production to a great extent.
So, do you need help in deciding which path fits your product? Then, let our engineering design services team review your component and help you choose the smartest approach.
Contact us at info@gighz.net for a free consultation today.
Latest Post
Get Customized Engineering CAD Design Service
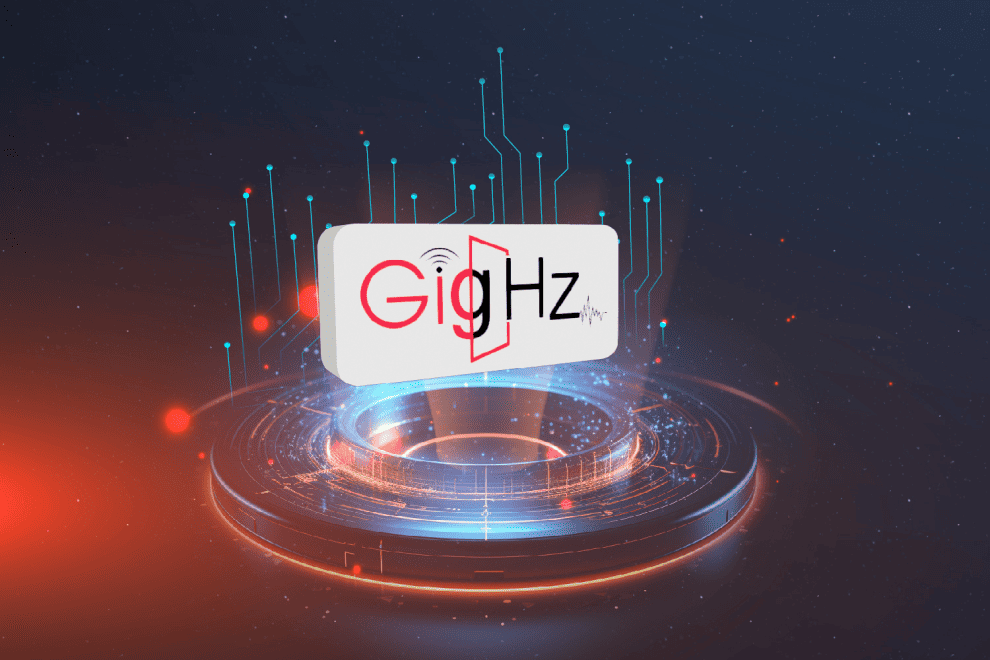
Book a Free Consultation Call​
Partner with Gighz and bring your most innovative design concepts to life. Our engineering cad services accelerate development so you can focus on your big vision.