7 Critical Considerations in Enclosure Design for Optimal Product Performance
- Posted On:
- June 20, 2025
- Category:
- Mcad
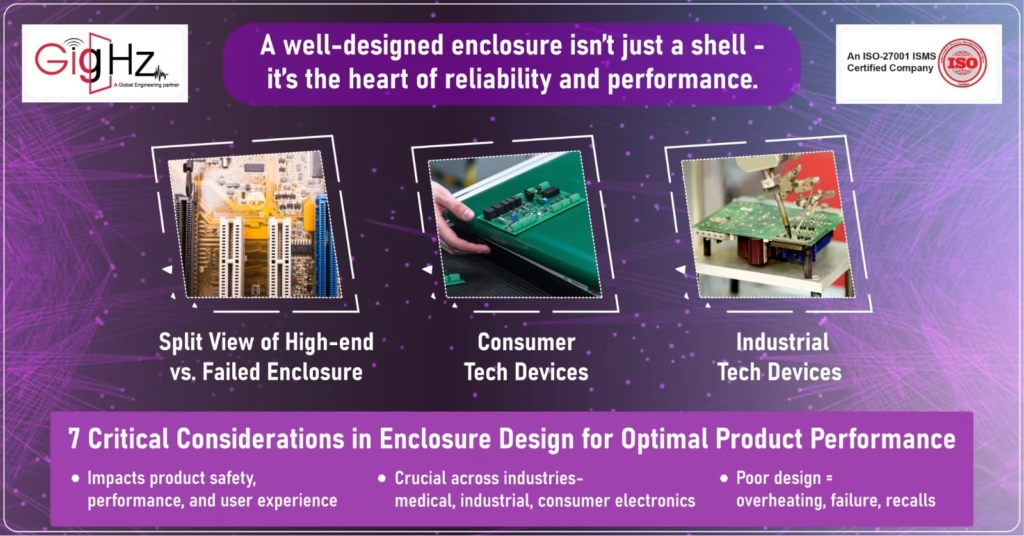
The enclosure’s design quality extends beyond basic protection because it’s the pillar of support for product reliability, product performance, and user experience quality.
The enclosure stands as an essential component, which enables both operational safety and commercial achievement for every device be it advanced medical machinery, industrial equipment, or consumer electronics.
Disregarding essential design considerations can lead to issues like product overheating, mechanical failure, regulatory non-compliance, and complete product recalls.
So, what differentiates an ordinary enclosure from an outstanding one?
In my decades of experience, the solution lies in detailed planning during the design stage.
Each decision made during the design stage related to manufacturing; be it material selection or thermal management affects the outcome of the final product.
The seven essential factors in enclosure design need attention from engineers and designers to reach peak performance levels.
1. Environmental Protection
Design choices for enclosures get essential direction from the fundamental conditions found in their operating environment.
Products that will operate outdoors must overcome distinct challenges compared to those designed for managed indoor settings.
Every product lifecycle requires knowledge about the distinct environmental hazards it must endure.
The IP (Ingress Protection) rating system enables standardized description of enclosure protection against moisture.
The IP67-rated enclosure found in Smartphone and fitness gadgets stops both dust from entering while also protecting against brief water submersion. Marine electronics together with food processing equipment need IP69K ratings to survive high-pressure and temperature washdowns.
Environmental resistance depends heavily on the selection of materials. Engineers must consider:
- Outdoor materials need UV stability to stop material degradation
- Chemical resistance for industrial or laboratory environments
- Corrosion protection for marine or high-humidity applications
- Thermal stability for extreme temperature variations
Different methods exist for material sealing depending on how well protection needs must be met. The level of weatherproofing determines which of the following sealing solutions will work:
- Double O-ring seals for critical waterproofing
- Complete component encapsulation requires potting compounds as a sealing method.
- Hermetic sealing for sensitive scientific instruments
2. EMI/RFI Shielding: Protecting Signal Integrity
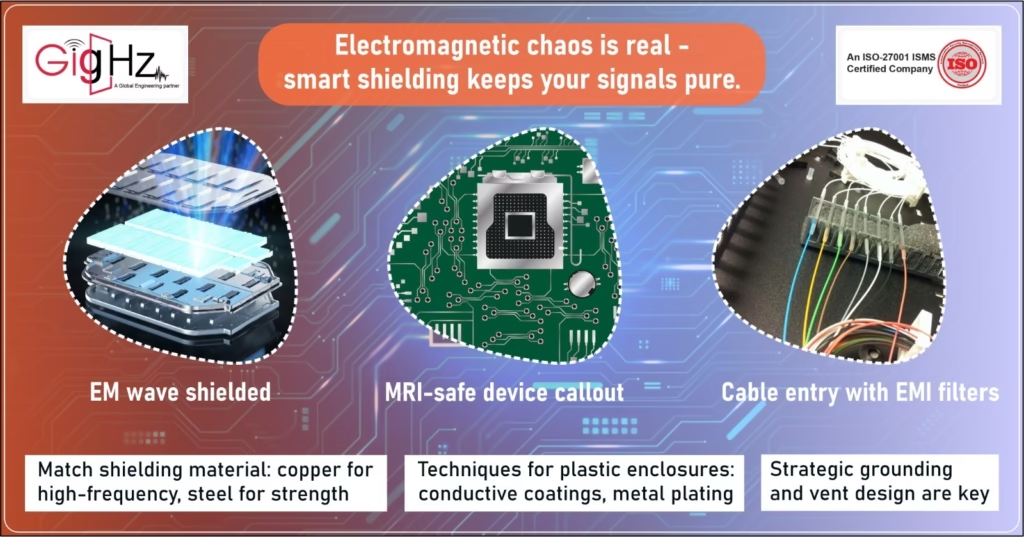
The surge of connectivity in our world has made electromagnetic compatibility emerge as a vital factor for design engineers.
Electronic devices require protection against external interference as well as from emitting interference.
The first step to achieve effective EMI/RFI shielding requires identifying the frequency bands, which potentially affect device operation.
The shielding ability of metal enclosures varies based on the material choice between aluminum and steel and copper and its alloys.
- The weight characteristics of aluminum enclosures match their effective general shielding properties.
- The excellent shield properties of steel come at the cost of substantial weight increase.
- High-frequency protection comes from copper as well as its alloy materials.
Engineers have multiple options to shield plastic enclosure, such as:
- Applying conductive coatings (nickel, copper, or silver-based)
- Using metalized plating material by vacuum deposition methods.
- Using conductive filler materials such as carbon fiber or metal flakes.
The grounding of components ensures the effectiveness of shielding. As an engineer, my comprehensive grounding approach includes:
- Low-impedance connections between shield components
- Accurate bonding of cable shields to enclosure grounds
- Positioning of the ground points strategically across various systems to stop ground loops.
The design of apertures becomes crucial because necessary ventilation openings, display connections, and connectors might reduce shielding effectiveness. Effective techniques include:
- Honeycomb vent patterns serve as blocking elements, which limit transmission of particular frequency ranges.
- Display windows should use conductive gaskets for their protection.
- Each cable penetration in the system requires EMI filters for installation.
There are numerous examples in the medical machinery industry that showcase successful shielding practices through its implementations. Special shielding solutions exist for MRI-compatible monitoring equipment enabling them to work in high-field environments and MRI scanners without disrupting image quality.
3. Thermal Management: Preventing Overheating Issues
A proper thermal management stands as a core enclosure design challenge; especially when consumers want smaller devices and electronic goods need increased power density. The initial step of proper thermal design requires accurate thermal modeling during the conceptual stage.
Reliability becomes an advantage when moving components are eliminated from passive cooling solutions.
- Heat sink integration with optimal fin geometry and orientation
- Using thermal interface materials, which have been specifically chosen for their conductivity properties
- Proper placement of vents by using natural convection currents for maximum effectiveness
- Phase change materials serve intermittent high-power applications.
Active cooling systems leverage better heat dissipation capabilities compared to other methods.
- Choosing fans that align airflow needs with acoustic noise requirements for optimal performance.
- Extreme thermal loads require liquid cooling loops to distribute heat across the system.
- Peltier devices for precise temperature control
Material selection determines how well thermal performance performs:
- Aluminum serves many applications because of its exceptional thermal conductivity properties.
- Plastics with thermal conductivity features allow designers to achieve reasonable heat transfer together with flexible use of materials
- Planar conductivity reaches exceptional levels when using graphite-based materials.
There are multiple examples of thermal innovation in the consumer electronics market. For example- modern gaming laptops implement advanced cooling mechanisms by utilizing two main thermal components.
- Vapor chamber heat spreaders
- Multiple heat pipe configurations
- Dynamic fan control algorithms
- Carefully engineered venting patterns
The systems prove that appropriate thermal design enables high performance retention within small physical dimensions.
4. Size and Form Factor: Optimizing Dimensions for Functionality
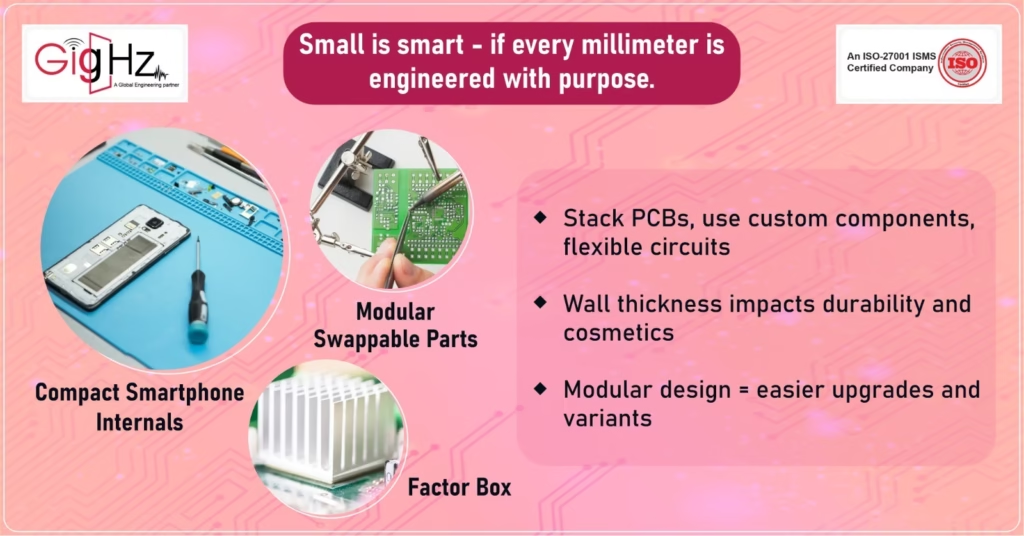
The physical dimensions and form of an enclosure directly affect usability together with manufacturability. The entire development process demands simultaneous management of various conflicting priorities to achieve effective form factor design.
The strategies used to place components determine how large an enclosure needs to be.
- Vertical space optimization can be done by stacking PCB to maximize enclosure dimensions.
- Custom component design methods enable maximum use of available space.
- Flexible circuit applications where appropriate
Optimizing wall thickness demands thorough evaluation because of its impact on product performance.
- A structural analysis will establish the absolute minimum thickness requirement for the component.
- The properties of materials used for molded parts need evaluation
- Cosmetic requirements for visible surfaces
The use of modular design approaches provides multiple benefits to designers.
- Simplified field upgrades and repairs
- Shared components across product lines
- Configurability for different market segments
For example- Smartphones illustrate exceptional space optimization techniques in the industry. The present-day flagship handsets reach high levels of internal space optimization by:
- Custom-shaped batteries
- Stacked motherboard designs
- Flexible circuit interconnects
- Advanced thermal management solutions
The innovative enclosure designs show that engineering creativity can break traditional size barriers to deliver improved functional performance.
5. Ease of Use: Designing for Assembly and Maintenance
Benefits of user-centric design approaches are beyond end consumers and also include manufacturing staff members and technicians. An accurate product enclosure design ensures smooth transactions and interactions in every life cycle stage.
Assembly optimization techniques include:
- Snap-fit features reduces the fastener count
- Self-locating parts for error-proof assembly
- The design includes easily accessible points for automated assembly operations.
Maintenance considerations should address:
- The design provides tool-less access to components which need regular maintenance services.
- Service documentation becomes visible on the product through part integration.
- Standardized fastener types throughout assembly
Service-friendly design can be observed through excellent examples from the automotive industry. Modern vehicle electronic control units show the following characteristics:
- Color-coded connectors
- Tool-less covers for field access
- Integrated diagnostic ports
- Clear component labeling
The designed features decrease maintenance service duration while minimizing possible errors that occur during servicing operations.
6. Safety Features and Regulatory Compliance
Every enclosure design needs safety considerations to run through it starting with the choice of materials and ending with mechanical characteristics. The regulatory framework keeps evolving specifically regarding products which could harm users.
Electrical safety features include:
- Adequate creepage and clearance distances
- Proper insulation barriers
- Secure strain relief for cabling
Mechanical safety considerations encompass:
- Rounded edges and corners
- Secure battery compartments
- Pinch point elimination
Material safety requirements may involve:
- Flame retardant ratings
- Chemical restriction compliance
- Toxicity limitations
Safety practices in the medical device sector show strict adherence to safety standards. Patient-connected equipment exemplifies:
- Double insulation systems
- Fail-safe mechanical interlocks
- Emergency disconnect features
- Comprehensive material biocompatibility
Product safety development techniques demonstrate the basic methods to embed safety into products.
7. Ergonomics and Aesthetics: Creating User Delight
Most products require a successful human-machine interface as their main success factor. The combination of technological specifications and human factor research produces effective product enclosure designs.
Ergonomic considerations include:
- Grip contour optimization
- Manufacturers should base control system position on measurements of human body dimensions.
- Tactile feedback design
Aesthetic considerations includes:
- Surface finish selection
- Brand identity integration
- Color and texture psychology
Consumer electronics showcase exceptional ergonomic integration. Modern game controllers demonstrate:
- Molded grips matching hand anatomy
- Button placement optimized for reach
- Variable trigger resistance
- Surface textures enhancing grip
Such characteristics work together to develop products with a smooth and intuitive interface.
Conclusion: Holistic Enclosure Design for Market Success
The development of exceptional enclosure design requires continuous attention to all the major factors from the beginning to the end of the process. Teams that successfully integrate these factors starting from initial concept development until production phase achieve the most successful products. Engineers who implement this complete design approach produce protective enclosures that boost performance while creating market-differentiating products that lead to better user experiences. Enclosure design development progresses through the emergence of new materials together with manufacturing techniques and market requirements. Forward-thinking organizations will advance all eight areas in order to develop the next generation of outstanding products.
CTA- Book Discovery Call
Are you ready to create a perfect enclosure design? Comments and let us know, if you need assistance or connect with our team on the below-mentioned link.
For more updates and enclosure design solutions follow us at-Â https://www.linkedin.com/in/chandra-thimma/
Latest Post
Get Customized Engineering CAD Design Service
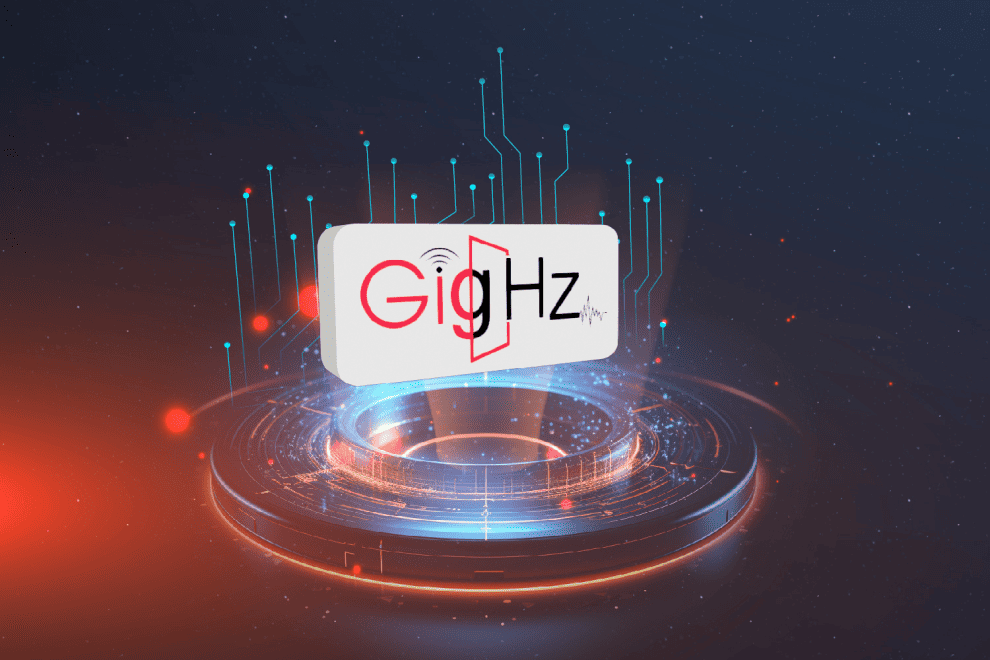
Book a Free Consultation Call​
Partner with Gighz and bring your most innovative design concepts to life. Our engineering cad services accelerate development so you can focus on your big vision.