Keep Your Pcb Enclosure Cool Not Hot!
Welcome Back!
Hope everything is going well.
In everyday language, we often use the term ‘heat’ to describe warmth, but scientifically, heat is defined as the transfer of energy from a warmer object to a cooler one.
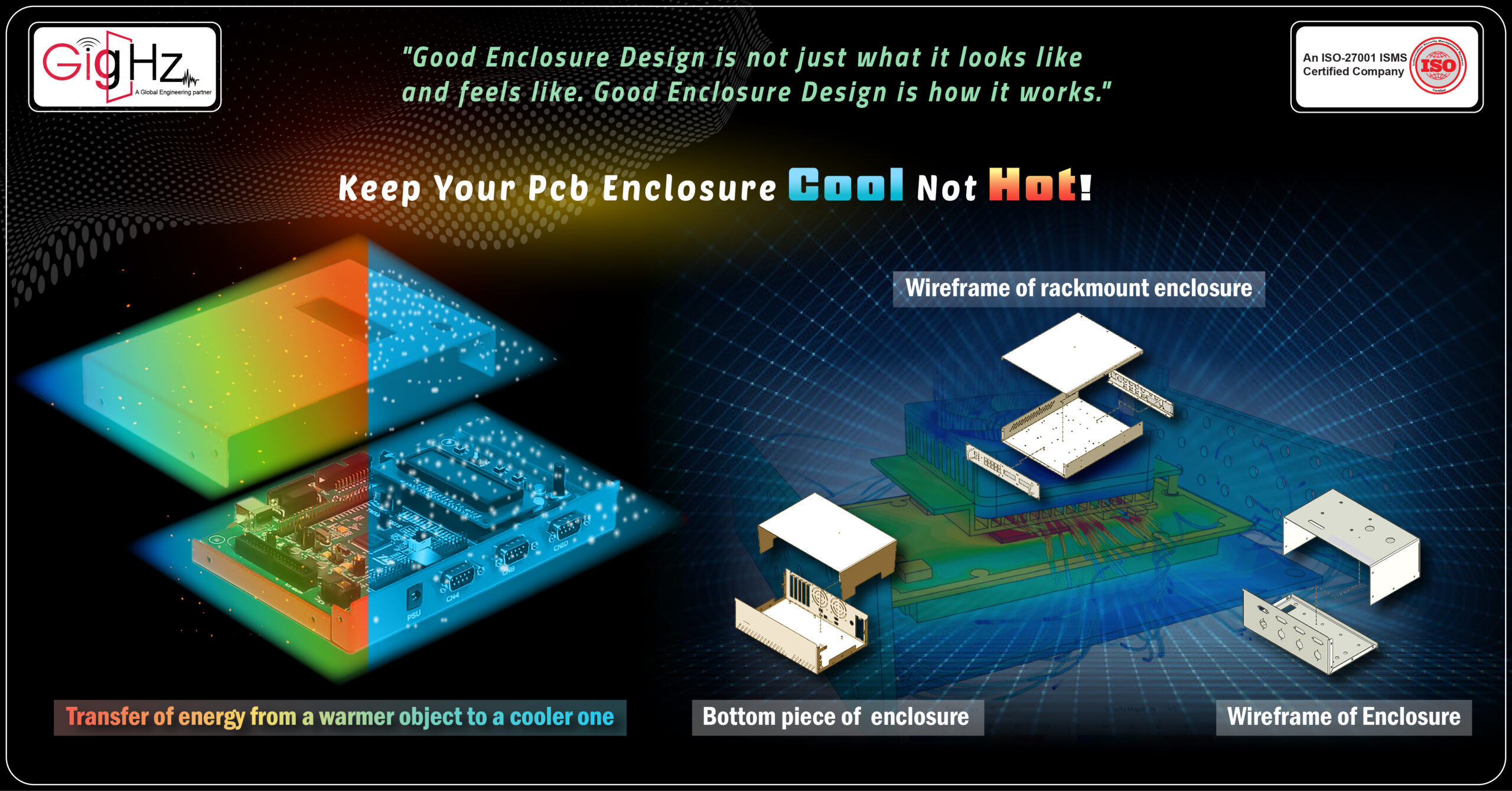
Welcome Back!
Hope everything is going well.
In everyday language, we often use the term ‘heat’ to describe warmth, but scientifically, heat is defined as the transfer of energy from a warmer object to a cooler one.
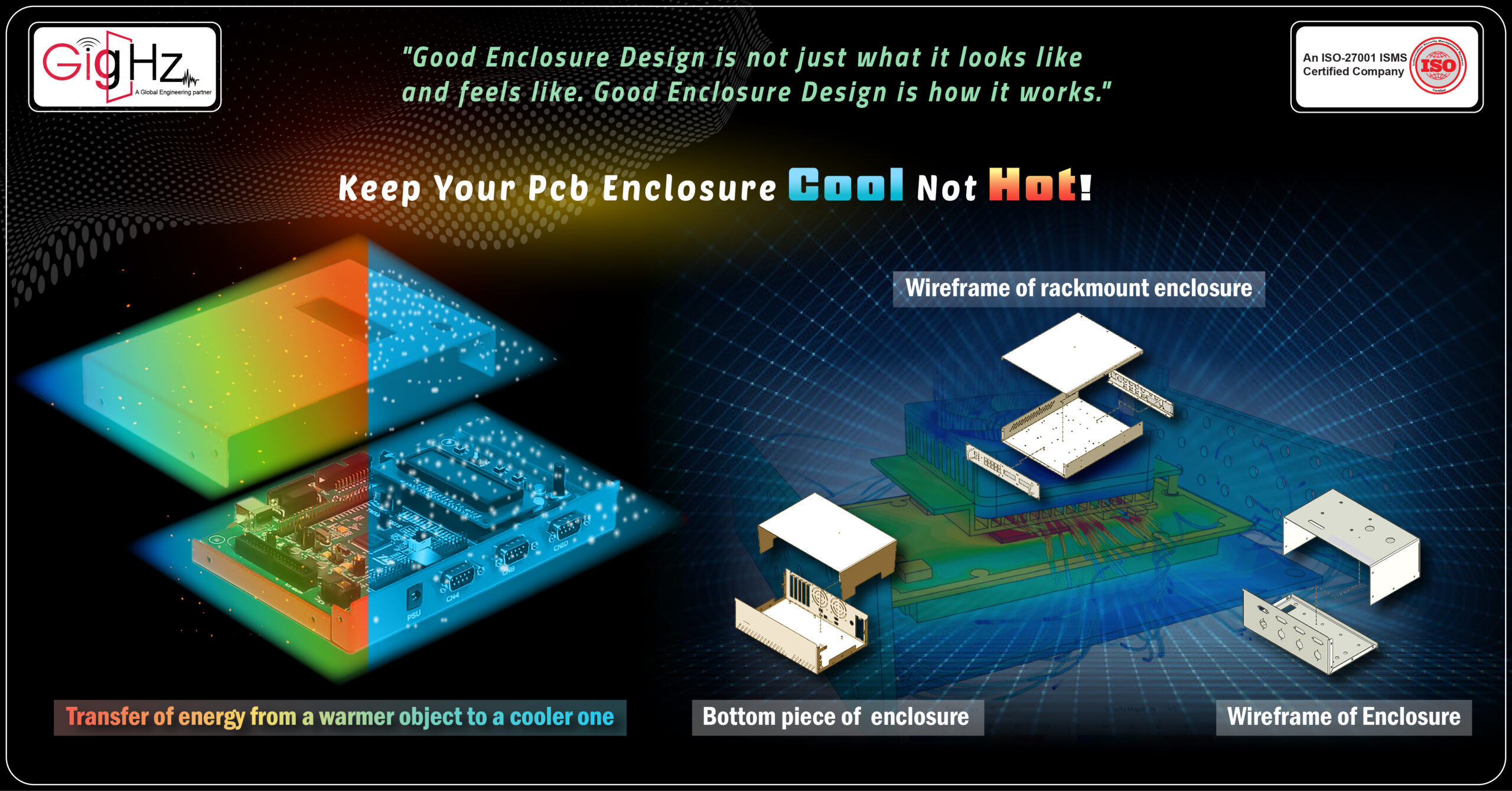
Category :
Published Date :
May 3, 2024
Category :
Published Date :
May 3, 2024
Category :
Published Date :
May 3, 2024
Heat is categorized into hot and cold based on this principle.
Heat energy surrounds us in various forms, whether it’s in icebergs, volcanoes, electronic devices or even within our bodies. Every substance contains heat energy within its structure.
The movement of tiny particles—atoms, molecules, or ions—in solids, liquids, and gases results in what we know as heat energy.
This energy can be transmitted from one material to another due to temperature variations between the objects, which we refer to as heat flow.
So, why here we are describing the heat, there is the reason behind these.
When it comes to some PCB enclosures just can’t handle the heat, literally!
Not all circuit boards crank out so much heat that they turn their enclosures into mini saunas, but when they do, it’s a problem.
Without a proper way to let that heat out, your components could end up feeling the burn.
There’s always a natural flow of heat from the hot bits to the cooler enclosure surface, but that flow needs an escape route to keep things in check.
So, if you’re aiming to design a PCB enclosure that won’t cook your components, here are some savvy strategies to save the day.
By making smart moves on both the enclosure and the PCB itself, you can kick that heat to the curb and maintain a chill vibe with the outside world.
Smart Moves to Beat the Heat in Enclosure
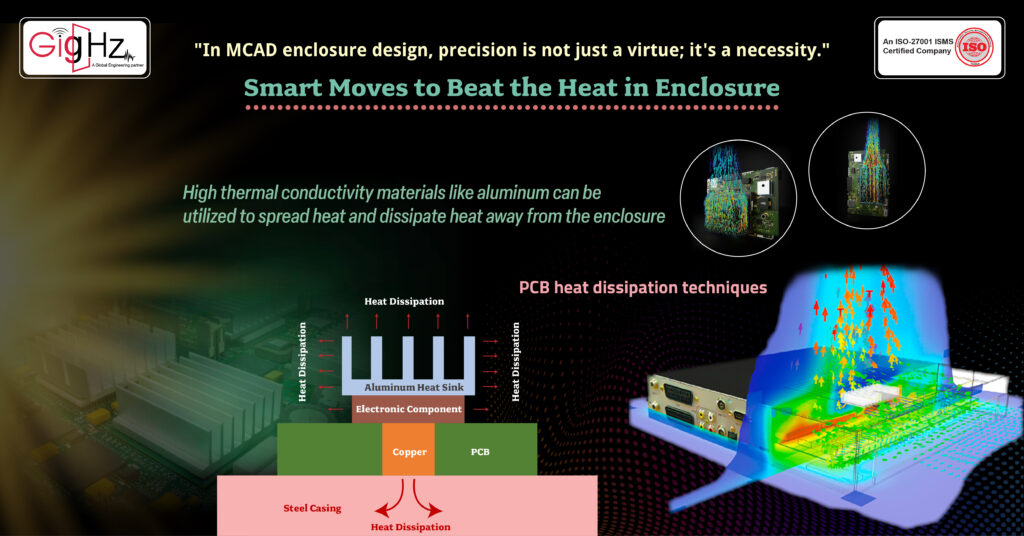
Key Info
Electrical engineering and mechanical techniques can be used to combat the extreme temperatures inside an enclosure.
Utilizing pcb heat dissipation techniques such as strategically placing heatsinks on hot components and incorporating heat exchange mechanisms can help move heat away from critical areas.
Additionally, employing convection to circulate hot air and designing the enclosure air flow can improve overall heat dissipation. High thermal conductivity materials like aluminum can be utilized to spread heat and dissipate heat away from the enclosure.
Advanced pcb design tools and design software can also aid in predicting and controlling heat generation and RF interference.
By implementing these smart moves, the temperature inside the enclosure can be effectively managed to prevent hot components from becoming hot to touch.
How do you spot this effect in your Enclosure?
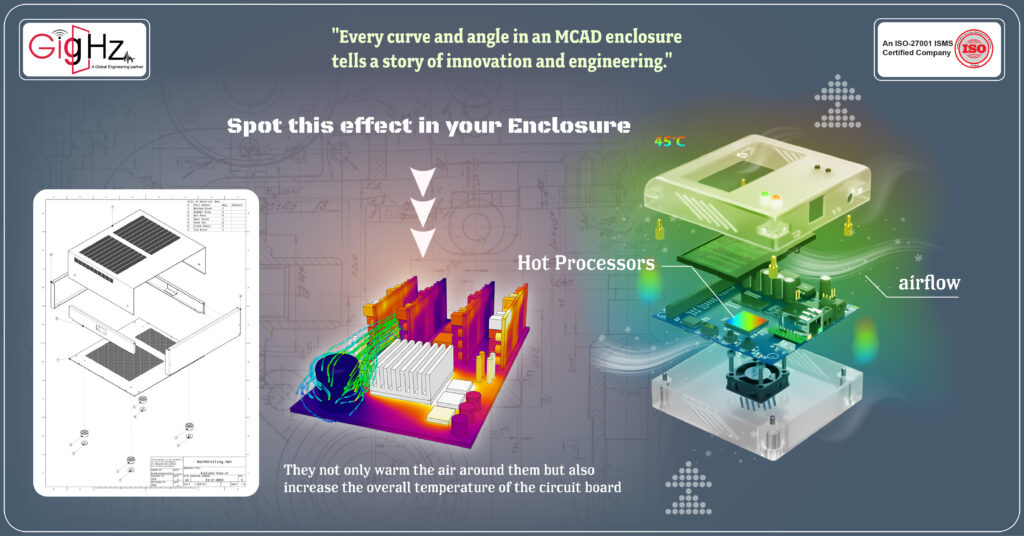
Some circuit boards can get really hot due to specific components like powerful processors, large FETs handling big currents, and high-current switching regulators that produce a lot of heat.
When these components heat up, they not only warm the air around them but also increase the overall temperature of the circuit board.
Without a case around the board, natural airflow helps cool things down a bit.
However, when you enclose the board, trapped hot air can turn the enclosure into a heat trap. The enclosure can become too hot to touch, which is inconvenient if people need to handle your product.
To identify when this heat buildup happens in your enclosure, you need to consider two main things:
Touch Test: If the product becomes too hot to touch at around 45°C in a normal room setting, it’s a sign you’re reaching uncomfortable temperatures with only a small safety buffer of 25°C.
Difference in Temperatures: Inside the enclosure, temperatures can be much higher than what you feel on the outside surface.
Even with a metal enclosure, the difference between what you touch and the internal temperature could be significant, around 20 to 25°C.
With insulating enclosures, this difference could be even greater.
Applying Measures to reduce the heat in PCB
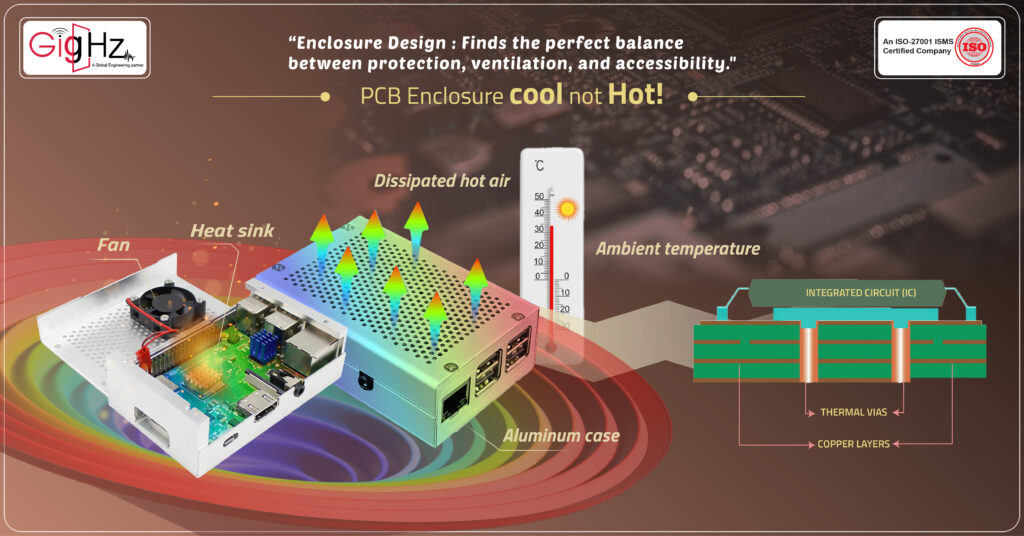
            Keep your PCB Enclosure cool not Hot!
When your enclosure gets sizzling hot and the internal temperature skyrockets, it’s all because the heat from the components can’t escape effectively.
Instead of heating up something with high thermal mass, like a heatsink, these components end up just warming the air around them.
While adding more copper to the PCB can help spread the heat a bit, it doesn’t solve the root cause of the oven effect, which stems from components heating the air around the board.
To tackle this issue, you need to get creative with both the board and enclosure designs:
- Incorporate grills or air holes for natural convection
- Install fans on the enclosure for forced cooling
- Attach a sizeable heat sink on the board connected to the enclosure
- Integrate heatsink fins onto the enclosure surface
- Enable external airflow over the outer enclosure
PCB thermal management is crucial in ensuring the reliability and performance of electronics housed in an electronic enclosure.
With ICs and microcontrollers generating high heat during operation, it is important to keep the printed circuit board cool to prevent hotspots and potential damage.
By incorporating cooling options such as heat sinks, thermal vias, and thermal pads into the pcb layout, heat can be effectively removed and dissipated.
Additionally, increasing the surface area for heat dissipation by using an aluminum enclosure or adding heat pipes can further improve thermal management.
However, if the enclosure is sealed, cooling options for sealed enclosures are limited. In such cases, heat exchangers or even an air conditioner may be necessary to prevent the enclosure design the heat load inside from increasing to a dangerous level.
When designing an enclosure, it is important to consider the ambient temperature and the amount of heat produced by the electronics heatsink at the edge of the PCB can help to prevent heat from building up in one specific area, while thermal vias can help conduct the heat to be dissipated throughout the printed circuit board.
By carefully planning the pcb assembly and implementing effective thermal management strategies, the risk of overheating and solder joints melting can be minimized.
Remember, a cooler PCB enclosure means better performance and longevity for your electronics.
Our Notable Upgrade: Engineering as a Service (EaaS)
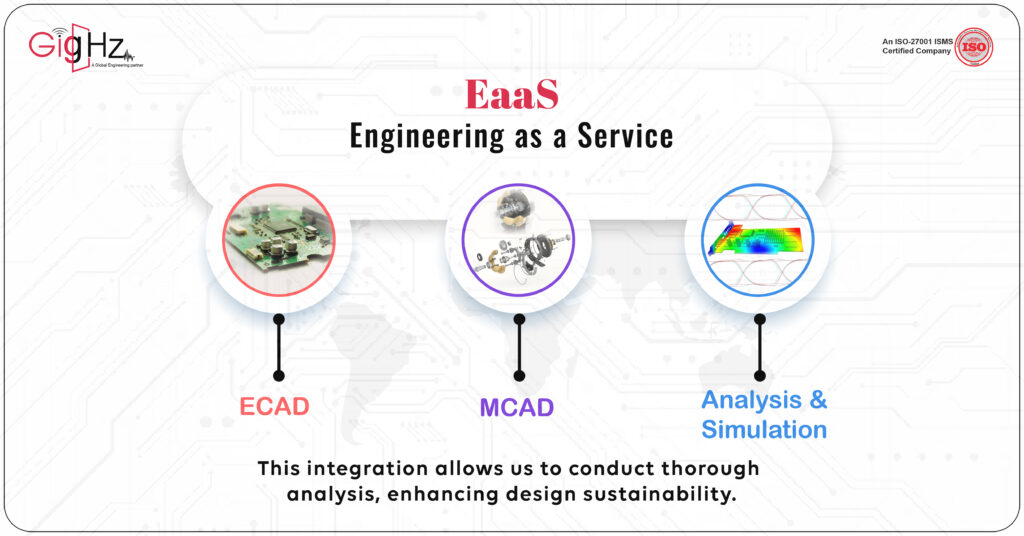
Absolutely!
The world of engineering is constantly evolving, and it’s fascinating to see how Engineering as a Service (EaaS) is keeping up with the demands of the industry.
By harnessing the power of ECAD, MCAD, and Analysis & Simulation, we’re able to provide comprehensive solutions that cover every aspect of the engineering process.
It’s really amazing how far we’ve come in terms of integrating different disciplines within engineering. With EaaS, we can seamlessly bring together electronic design, mechanical design, and analysis and simulation, all under one roof.
This not only saves time but also improves efficiency and collaboration among engineers.
Conclusion
When working on a project that involves electronics, it is crucial to consider the thermal aspects of the design and lay out a plan to transfer heat effectively.
The key PCB components such as ICs often remove heat and can get quite hot, requiring thermal solver design techniques to ensure they stay within a safe operating temperature.
By using the best dissipation techniques like internal copper and finned heat sinks, the excess heat produced by these components can be transferred to the outside of the enclosure.
The enclosure is made of materials that can handle the thermal stress and keep the electronics cool. Thermal analysis is a crucial part of the electrical and mechanical product design process to ensure the working product does not overheat.
Additionally, placing components near the edge or a side of the board can help with heat needs and transfer heat more efficiently. In some cases, an air conditioner solution may be necessary to keep the electronics cool in demanding environments.
By utilizing thermal solver design techniques properly, you can ensure that your product stays within its operating temperature limits and avoids any thermal stress that could impact its performance.
Start Your Success Journey – Book a Call! https://calendly.com/gighz/30min