Challenges faced in Electronic Design Automation (EDA) conversion
- Posted On:
- July 18, 2024
- Category:
- Ecad
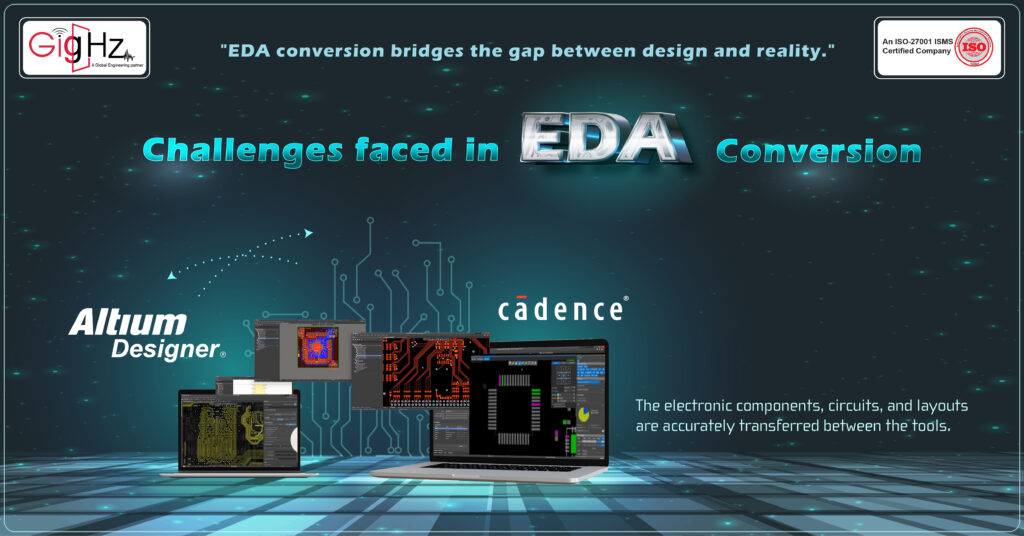
Electronic Design Automation(EDA) Conversion
Imagine you have two different computer programs used by engineers to design electronic devices like smartphones or computers. These programs store and interpret design information in slightly different ways.
This is where EDA Conversion steps in — it acts like a translator, converting the design data from one program into a format the other program can easily understand.
In simple terms, EDA Conversion ensures that essential details about the electronic components, circuits, and layouts are accurately transferred between the tools. This allows engineers to work across different software platforms, collaborate more efficiently, and develop electronic designs without issues.
In the fast-paced world of automotive PCB design, an example of EDA conversion in action would be the transition from Altium to Cadence tools when designing an Electronic Control Unit (ECU) for a next-generation electric vehicle. This conversion is crucial for:
- Streamlining Design Tasks: It reduces time spent reworking data to make it compatible across platforms.
- Enhancing Collaboration: Multiple teams using different software can still collaborate on the same design without compatibility issues.
- Ensuring Seamless Integration: It ensures that all electronic components and circuits work together as intended, optimizing the performance of the vehicle’s electrical system.
By using EDA conversion, engineers can overcome challenges related to tool compatibility and improve project outcomes, ultimately making the design process more efficient and precise. This practical application ensures that the final ECU design is ready for production, meeting both functional and performance requirements of the electric vehicle.
CAD Translation Workflow – Our Process
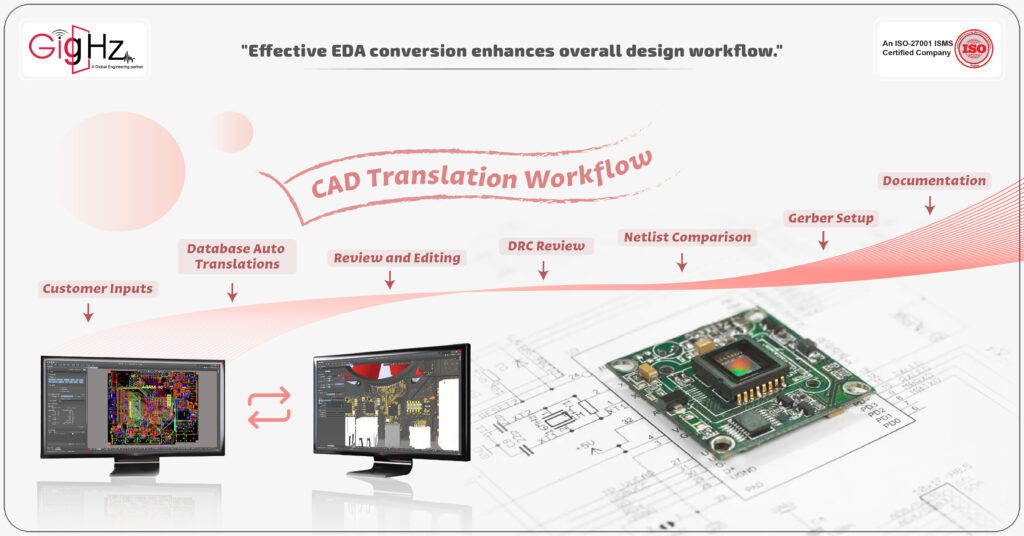
Customer Inputs: GigHz begins the CAD translation workflow by gathering essential customer inputs, including the PCB database, which consists of:
- Schematics
- Layout
- Libraries
- Bill of Materials (BOM)
- Design Rule Check (DRC) rules
- Layer stack-up
- Templates for documentation.
PCB Database Auto Translations: We utilize the necessary toolchain to automate the translation of the PCB design database. This ensures a smooth and seamless integration with the required EDA tool, saving time and minimizing manual effort.
Review and Editing: After the auto-translation, our team conducts a thorough review and editing of the translated schematics and layout. This step ensures that any properties lost during the translation process are corrected for accuracy, guaranteeing that the design matches the original intent.
DRC Review: A comprehensive Design Rule Check (DRC) is performed to identify and correct any discrepancies or violations within the translated design. This ensures the design complies with specified rules and standards, meeting all the necessary requirements for the target EDA platform.
Schematic and Layout Netlist Comparison: GigHz performs a detailed comparison of the schematic and layout netlists, ensuring consistency and accuracy across all design elements. This step helps identify any mismatches between the design representations.
Gerber Setup: The Gerber setup is modified and optimized based on the original project specifications. This step ensures that the translated design is fully aligned with the fabrication and manufacturing processes, helping to minimize errors during production.
Documentation and Release: The final step involves preparing comprehensive documentation, which organizes and details all translated CAD data. This ensures a smooth transition to the desired EDA platform, providing clients with organized information that supports continued development and production.
Challenges faced in Electronic Design Automation(EDA) conversion
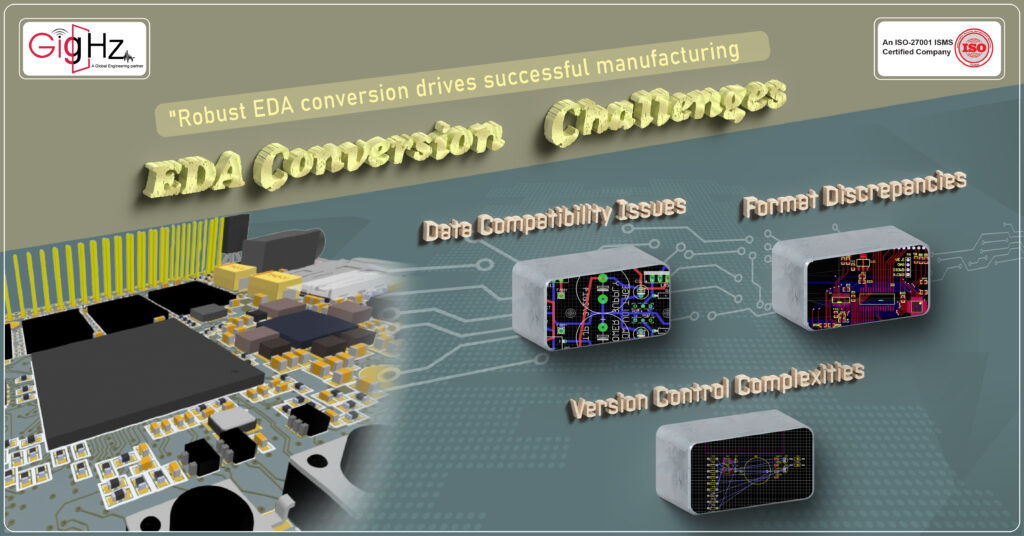
Data Compatibility Issues
- Challenge: Incompatible data formats between Altium and Cadence tools impede the seamless transfer of design data, leading to potential errors and discrepancies in data interpretation.
- Impact: Delays in data exchange, loss of design integrity, and inefficiencies in integrating design elements between Altium and Cadence environments.
Format Discrepancies
- Challenge: Varied design formats in circuit diagrams, layouts, and component information between Altium and Cadence introduce complexities in translating design specifications accurately during collaboration.
- Impact: Miscommunication, design errors, and inconsistencies in design representations hinder the accuracy and functionality of the ECU development project.
Version Control Complexities
- Challenge: Managing multiple design versions between Altium and Cadence manually results in version control discrepancies, making it challenging to maintain an accurate design history and track revisions.
- Impact: Confusion in version tracking, lack of traceability, and potential errors in design modifications compromise the integrity of the ECU development process.
Implementing EDA Conversion Solutions
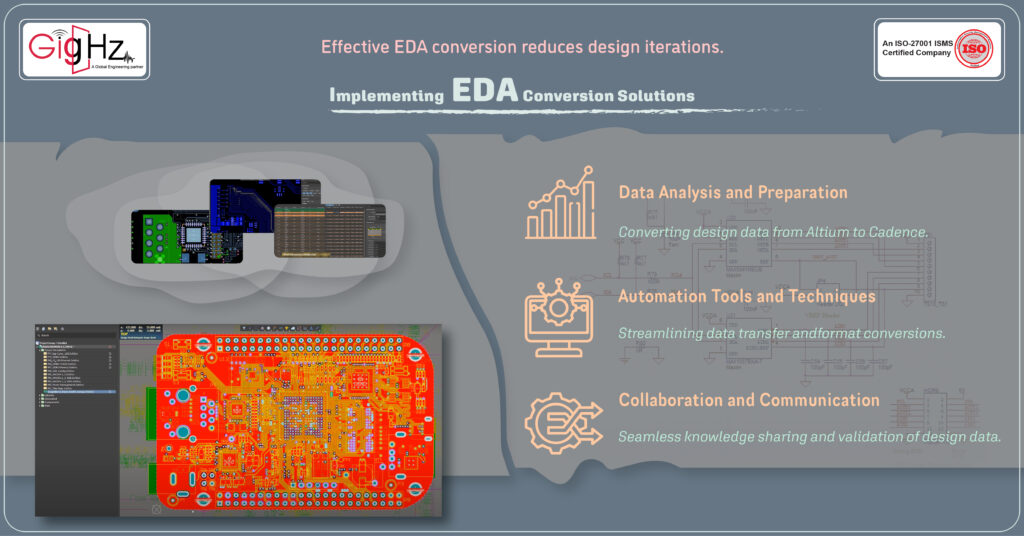
Data Analysis and Preparation
- EDA Conversion Tools: Utilizing specialized tools for converting design data from Altium to Cadence, ensuring data normalization, and maintaining consistency in design structures.
- Pre-Migration Assessment: Conducting thorough data analysis to identify format discrepancies, clean data, and prepare it for seamless migration between Altium and Cadence platforms.
Automation Tools and Techniques
- Automated Migration Workflows: Implementing automated migration workflows tailored for the conversion from Altium to Cadence, streamlining data transfer, format conversions, and version control management.
- Validation Procedures: Employing automated validation checks to verify data accuracy, integrity, and compliance with automotive design standards post-conversion from Altium to Cadence.
Collaboration and Communication
- Cross-Platform Collaboration: Encouraging collaboration among engineers using Altium and Cadence tools, enabling seamless knowledge sharing and validation of design data.
- Clear Communication Channels: Establishing clear communication channels to address challenges, share insights, and coordinate efforts effectively throughout the EDA conversion process from Altium to Cadence.
Transforming Automotive PCB Design with Altium to Cadence EDA Conversion
- By harnessing the power of EDA conversion from Altium to Cadence in automotive PCB design, our hypothetical automotive electronics company successfully overcomes data compatibility challenges, mitigates format discrepancies, and enhances version control practices tailored to these specific EDA tools.
- This real-time application exemplifies how EDA conversion optimizes design workflows, fosters collaboration, and drives innovation in developing cutting-edge automotive electronic systems, emphasizing the strategic importance of seamless data transfer and integration between Altium and Cadence environments for achieving design excellence in automotive PCB projects.
Design Data Translation: 100%
We offer EDA conversion services to global clients, ensuring that the resulting translation is complete and maintains the integrity of the original data.
Using various EDA techniques to migrate design data from legacy design data to the current EDA platform, the company has expertise in electronic design automation and can migrate any of your CAD systems or ECAD platforms to any current EDA platform.
With a focus on logical and functional aspects of your design, Design Data Translation: 100% has explored different EDA platforms such as Eagle, Mentor, Zuken, and more to offer EDA conversion services for all your electrical and packaging needs.
Conclusion
The highlights the significance of utilizing advanced EDA software to facilitate the swift and efficient migration of designs across different CAD systems.
With our vast experience in migrating designs from many platforms, we understand the importance of preserving data integrity and ensuring seamless transition of CAD data across various engineering company setups.
By leveraging the capabilities of EDA platforms, companies can significantly reduce their workload and improve overall efficiency in the design and verification process.
Furthermore, these EDA platforms not only generate accurate output data but also provide services to its global enterprise clientele, thereby streamlining the design flow and enhancing collaboration among various MCAD and EDA tools.
In conclusion, the adoption of advanced technology in EDA software is essential for any current engineering company looking to stay ahead in the competitive market and drive innovation in their products.
Discover our Specialities. Visit our Services Page. https://gighz.net/eda-conversion-services/
Table of Contents
Latest Post
Get Customized Engineering CAD Design Service
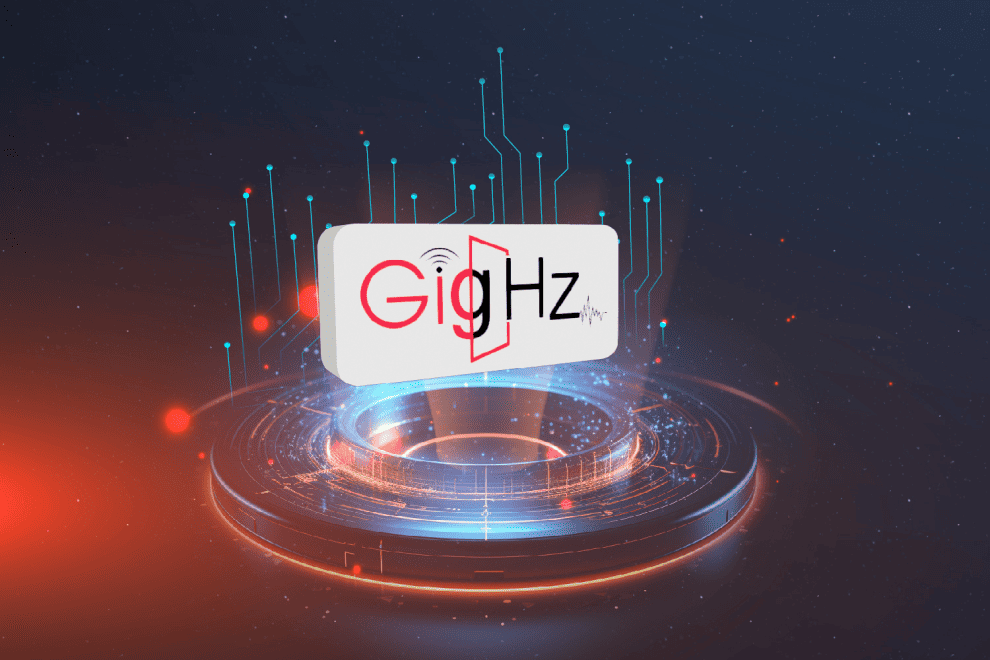
Book a Free Consultation Call​
Partner with Gighz and bring your most innovative design concepts to life. Our engineering cad services accelerate development so you can focus on your big vision.