7 challenges make risky Towards Sustainable Automotive PCB Design
- GigHz
- February 6, 2025
- emi and emc
- Home
- Email Us
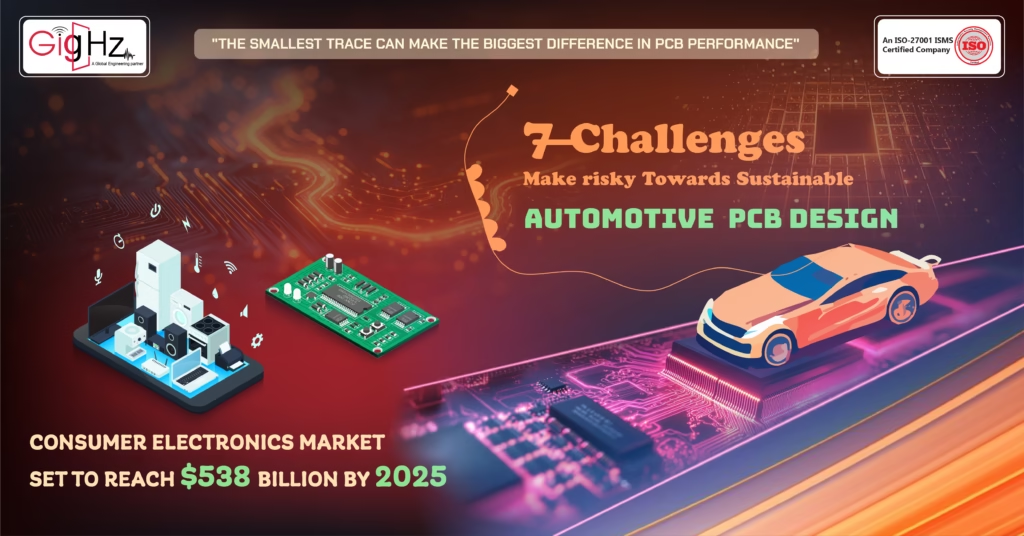
Sustainable Automotive PCB Design
Have you ever thought about how sustainable the word sustainable truly is?
Sustainability is now a major focus in engineering and manufacturing, and it’s only going to grow as companies and countries work toward the United Nations’ sustainability goals.
But here’s the thing:
While PCBs have been made the same way for years, the process is energy-intensive, creates toxic wastewater, and leads to a huge amount of electronic waste.
Think about it,
Advances in PCB technology have fueled the evolution of high-end consumer electronics like smartphones and gaming consoles.
And with the consumer electronics market set to reach $538 billion by 2025, the demand for eco-friendly PCB production will only increase.
That’s why some forward-thinking engineers are already exploring ways to make PCBs more sustainable, both in design and manufacturing, to help reduce the environmental footprint.
Now, let’s look at where the world is heading in PCB design,
Companies are now looking into biodegradable and recyclable materials for PCBs, reducing the environmental impact and waste after their lifespan.
Using less energy, minimizing greenhouse gas emissions and aligning with global energy-efficiency goals.
Pushing for products that last longer, modular PCB designs allow easier repair and component replacement, extending the lifecycle of devices and reducing e-waste.
It’s an exciting step toward electronics that not only advance technology but also protect the environment.
7 challenges makes risky Towards Sustainable PCB Design
1. Tough Conditions – Can Sustainability Survive the Heat?

Automotive PCBs are built to handle a lot.
Automotive electronics operate in some of the harshest environments—extreme temperatures, intense vibrations, and constant exposure to oil, fuel, and humidity.
Switching to sustainable materials, such as halogen-free laminates or bio-based substrates, introduces a challenge: can they endure these demanding conditions? Many eco-friendly options aren’t designed for the heat and mechanical stress found in engine compartments or battery packs, making durability a critical concern.
2. Safety First – Does Sustainability Pass the Crash Test?
In automotive electronics, safety isn’t optional—it’s mandatory. Systems like Advanced Driver Assistance Systems (ADAS) and Battery Management Systems (BMS) must meet stringent standards like ISO 26262 for functional safety because failure isn’t just inconvenient—it’s catastrophic.
The problem? Many sustainable PCB materials haven’t been fully tested under real-world automotive conditions.
- Can they withstand flame, heat, and long-term stress?
- Do they maintain consistent performance over time?
Sustainability must prove it can match the reliability of traditional materials—because in automotive electronics, safety always comes first.
3. Material Switch – Is This the Right Fit for Complex Designs?
Automotive PCBs are complicated.
The design is often highly integrated, managing power, signals, and even complex data between various systems.
Swapping traditional PCB materials for sustainable alternatives—like bio-based laminates or recyclable substrates—requires in-depth testing to ensure signal integrity isn’t compromised, and thermal dissipation remains optimal.
Can these eco-friendly materials handle the complexity of modern automotive design without introducing noise, latency, or thermal issues?
You need to make sure your sustainable choice doesn’t end up as a weak link in the design chain.
4. The Price of Going Green – Is the Initial Investment Worth It?

Sustainable materials often come with a price tag.
Sure, there are long-term environmental benefits—less waste, reduced carbon footprint, and potentially lower disposal costs—but the upfront investment can scare some manufacturers.
The reality is, automotive PCBs are already a cost-sensitive part of vehicle design. Moving to sustainable materials means investing in R&D, new suppliers, and potentially higher production costs.
The question is: can the industry make the math work, especially in low-cost vehicle markets?
5. Manufacturing – Can You Scale Sustainable Production?
Manufacturing eco-friendly PCBs requires different techniques, like additive manufacturing (think 3D printing) or laser drilling.
These methods offer precision, but they aren’t yet scalable for high-volume automotive production. What happens when you need to produce millions of PCBs for the latest electric vehicle model?
These processes may not yet be ready to meet the high-volume, high-speed demands of the automotive industry.
Plus, incorporating these new techniques into existing production lines can be a costly and time-consuming transition.
Can the supply chain adapt to handle this?
6. Limited Material Choices – Where Do You Source Your Green Materials?

Another challenge? Sourcing sustainable materials in bulk. Right now, materials like halogen-free laminates or biodegradable substrates are still niche. That means availability is limited, and prices can fluctuate. When you’re designing a vehicle, especially at scale, supply chain stability is critical. If you don’t have reliable access to these materials, you risk production delays or cost hikes. Are there enough suppliers to meet the growing demand for sustainable materials at scale?
7. End-of-Life – What Happens to Sustainable PCBs After Use?
Recycling is a big win for sustainability—but it’s also a challenge. Automotive PCBs often end up as e-waste, and the recycling systems for sustainable materials aren’t fully developed yet. Some eco-friendly materials might actually be harder to recycle than conventional ones due to the complexity of their chemical composition. So, while we’re working toward greener designs, we’re still dealing with the fact that at the end of the car’s life cycle, those PCBs could end up in landfills unless we improve recycling processes. Can we design truly sustainable vehicles if we haven’t solved the recycling puzzle yet?
Conclusion
The advancement of pcb manufacturing processes is crucial for the electronics industry to achieve sustainability goals.
By adopting sustainable practices such as utilizing recycling programs and incorporating environmentally friendly materials like cellulose and lead-free solder, manufacturers can significantly reduce waste.
The shift from traditional pcbs to more innovative designs allows for enhanced reliability and longevity of circuit boards.
Connect with us on LinkedIn for more interactive insights https://www.linkedin.com/company/3483128/
Â
Latest Post
Get Customized Engineering CAD Design Service
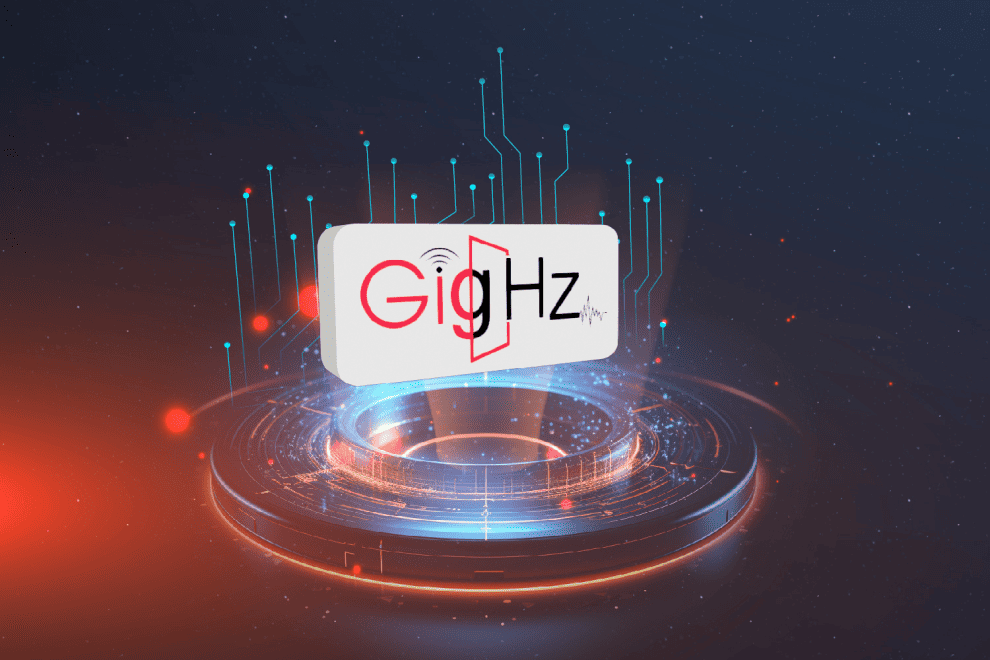
Book a Free Consultation Call​
Partner with Gighz and bring your most innovative design concepts to life. Our engineering cad services accelerate development so you can focus on your big vision.