How to Achieve Unmatched Power Integrity Analysis in PCB Designs?
- Posted On:
- September 27, 2024
- Category:
- Analysis & Simulation
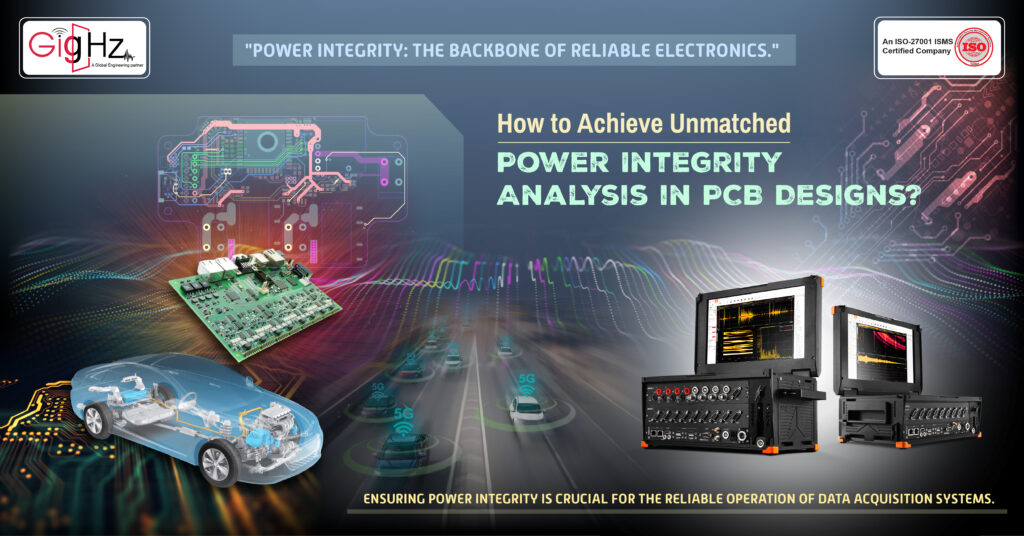
PCB Power Integrity Analysis
In today’s cars, data acquisition systems are like high-tech sensors that keep track of what’s happening inside and outside the vehicle.
They monitor important details such as engine performance, speed, fuel use, and even weather conditions to help make sure everything runs smoothly.
These systems help car manufacturers and drivers by providing real-time information about how the car is performing.
If the engine is running too hot or if there’s a problem with fuel efficiency, the system can alert the driver or make adjustments to keep things running properly.
This makes cars safer and more reliable.
With data acquisition systems, car makers can spot potential problems before they become serious issues.
This helps prevent breakdowns and can improve the car’s overall performance and durability.
It also helps ensure that advanced safety features, like automatic braking and lane-keeping assist, work correctly.
The system collects data from sensors installed all over the car.
This data is then used to monitor and control different aspects of the vehicle in real-time.
It can adjust fuel usage or activate safety features based on the data it receives.
This helps keep the car running efficiently and safely.
Ensuring power integrity is crucial for the reliable operation of data acquisition systems.
Power integrity analysis focuses on maintaining stable and clean power supply to the system’s components.
Let’s dig in for more details!
How to Achieve Unmatched Power Integrity Analysis in PCB Designs?
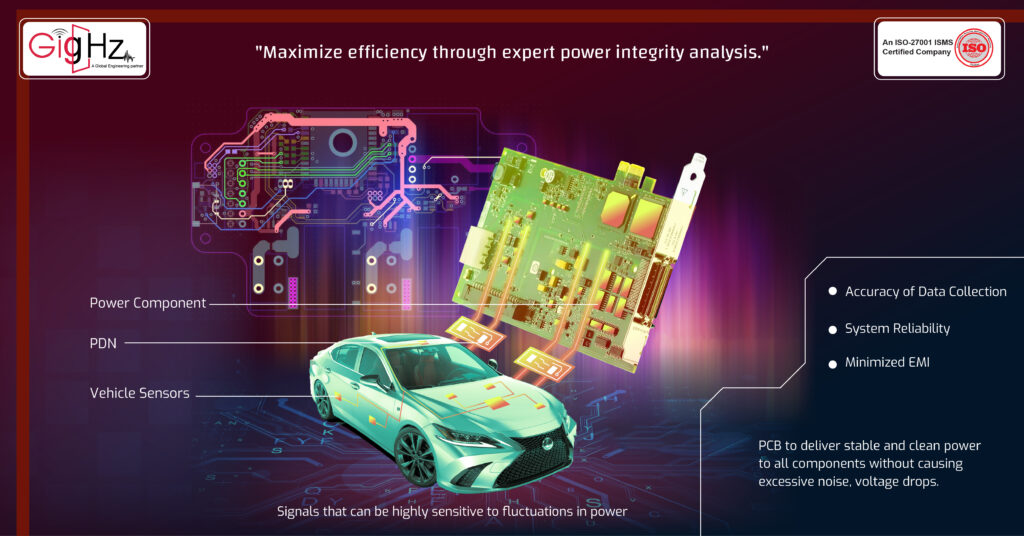
Power integrity refers to the ability of the power delivery network (PDN) on a PCB to deliver stable and clean power to all components without causing excessive noise, voltage drops, or interference. For data acquisition boards, which are responsible for collecting and processing signals from multiple sensors, maintaining power integrity is critical to ensure the accuracy and reliability of the data.
Power Integrity Importance in Data Acquisition Systems
Accuracy of Data Collection: Data acquisition boards process signals that can be highly sensitive to fluctuations in power. Even minor disruptions in power supply can lead to inaccuracies in data collection, resulting in faulty readings that can compromise the vehicle’s performance and safety.
System Reliability: High power integrity ensures that the data acquisition system operates reliably under various conditions. This reliability is crucial for advanced automotive functions like engine control, fuel management, and safety systems, where consistent and accurate data is paramount.
Minimized Electromagnetic Interference (EMI): Poor power integrity can lead to increased electromagnetic interference, which can corrupt data signals and cause malfunctions. A well-designed power distribution network helps minimize EMI, ensuring that the data acquisition board operates efficiently without affecting other vehicle systems.
Power Integrity Analysis in PCB Design
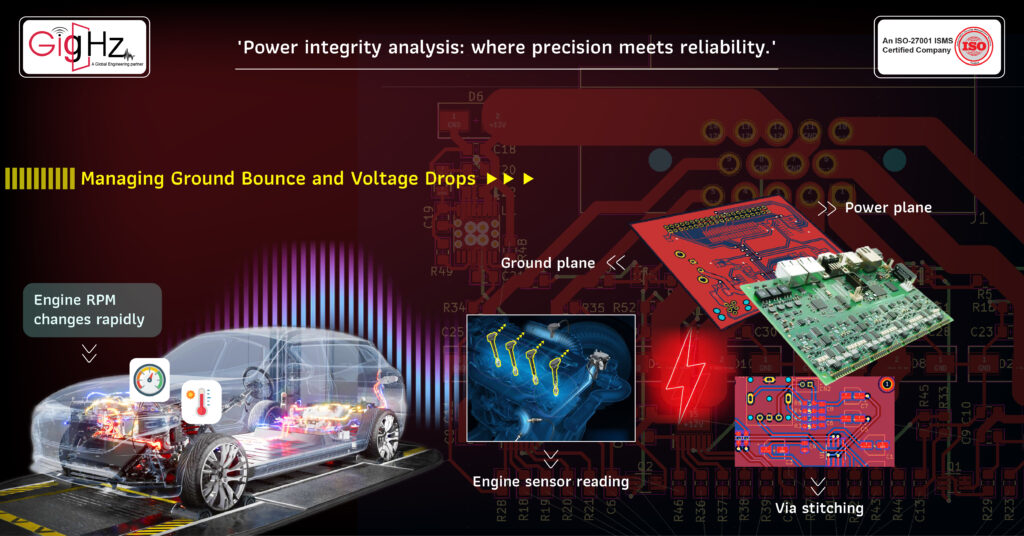
Power Delivery Network (PDN) Design
In a data acquisition board that monitors engine parameters such as temperature, pressure, and RPM, the stability and cleanliness of the power delivery network (PDN) are crucial. If the PDN is not properly designed, voltage drops and noise can interfere with the precise signals from sensors, leading to inaccurate readings of these critical engine parameters.
The PDN should include well-designed power planes and strategically placed decoupling capacitors to filter out noise. Wide power traces should be used to handle the current demand without causing significant voltage drops. By ensuring a robust PDN, the board can maintain stable power levels, preventing errors in temperature, pressure, and RPM measurements.
Managing Ground Bounce and Voltage Drops
When the engine RPM changes rapidly, or when there is a sudden variation in engine pressure or temperature, ground bounce can occur, causing fluctuations in the ground voltage.
These fluctuations can lead to errors in the data acquisition system, resulting in incorrect sensor readings.
To prevent ground bounce, the ground plane must be designed to provide a continuous, low-impedance path. Additionally, via stitching can help to reduce impedance and ensure that the ground potential remains stable, thus preventing errors in the measurement of engine temperature, pressure, and RPM due to fluctuating ground voltage.
Signal Integrity and Power Integrity Co-Design
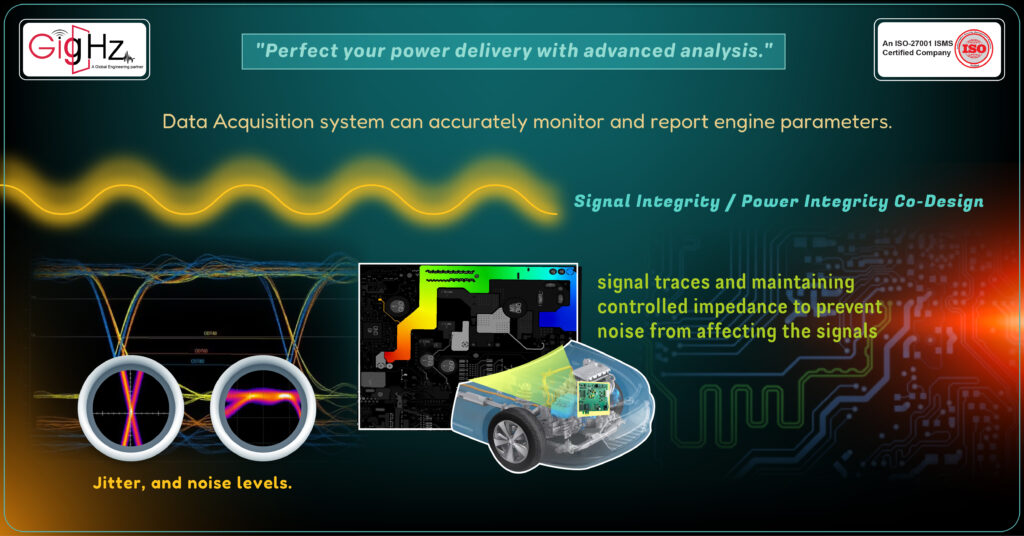
The accuracy of signals corresponding to engine parameters is crucial for the proper functioning of the data acquisition system. If power integrity is compromised, it could lead to signal integrity issues like jitter or timing errors, which could distort these critical sensor readings.
To avoid such issues, signal integrity and power integrity must be co-designed. This involves careful routing of signal traces and maintaining controlled impedance to prevent noise from affecting the signals. By ensuring that power integrity supports signal integrity, the data acquisition system can accurately monitor and report engine parameters.
Simulations and Analysis Techniques
Before deploying the data acquisition board in the vehicle, simulations can predict how the PDN will perform under varying engine conditions—such as fluctuations in temperature, pressure, and RPM.
These simulations can help identify potential issues like voltage drops or excessive noise that could distort sensor readings.
Power integrity simulations and analysis techniques, such as impedance analysis and Time-Domain Reflectometry (TDR), can be used to assess the PDN and ensure it meets performance requirements.
By addressing potential problems during the design phase, you can ensure that the data acquisition board will accurately monitor engine parameters like temperature, pressure, and RPM without being affected by noise or voltage fluctuations.
Final Thoughts
Journey through the power distribution network reveals the critical role of power and ground management in achieving good power integrity within high-speed designs. Understanding the basics of power integrity allows a PCB designer to craft a robust system design that accommodates both AC and DC power requirements. Utilizing advanced PCB design software and analysis tools, designers can effectively perform power integrity analysis on the PCB’s power delivery network to identify and rectify power integrity problems.
Employing a power rail probe during the PCB layout phase enables the assessment of signal and power integrity, ensuring that the power rail can provide power efficiently. As we delve deeper into high-speed design, it becomes essential to analyze power distribution strategies that not only meet performance expectations but also mitigate risks associated with AC power integrity. The PCB editor’s support for power analysis enhances the design system, ultimately leading to a more reliable and efficient board design.
Book a Time to Discuss Your Needs! https://calendly.com/gighz/30min
Table of Contents
Latest Post
Get Customized Engineering CAD Design Service
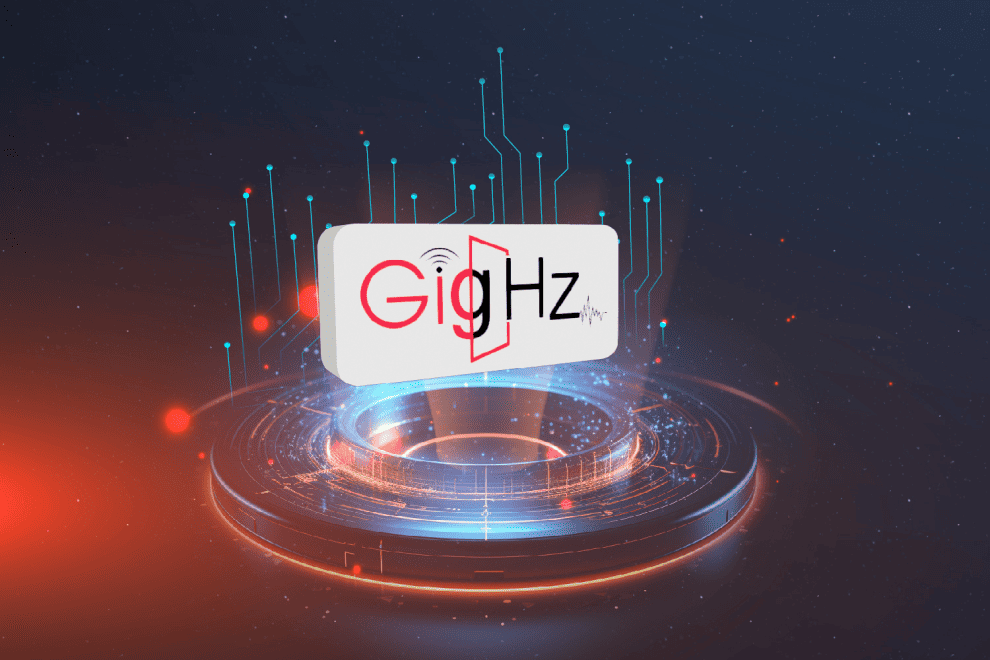
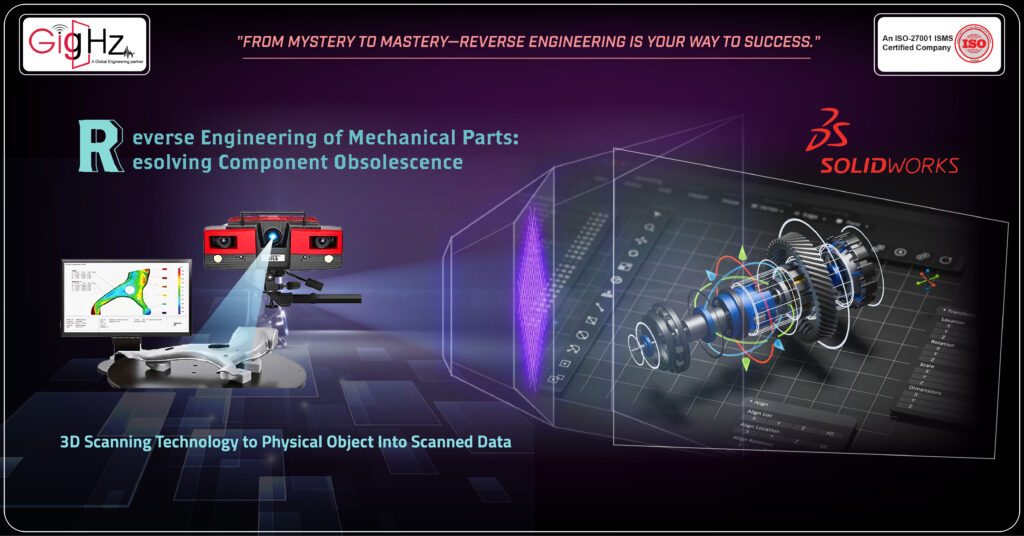
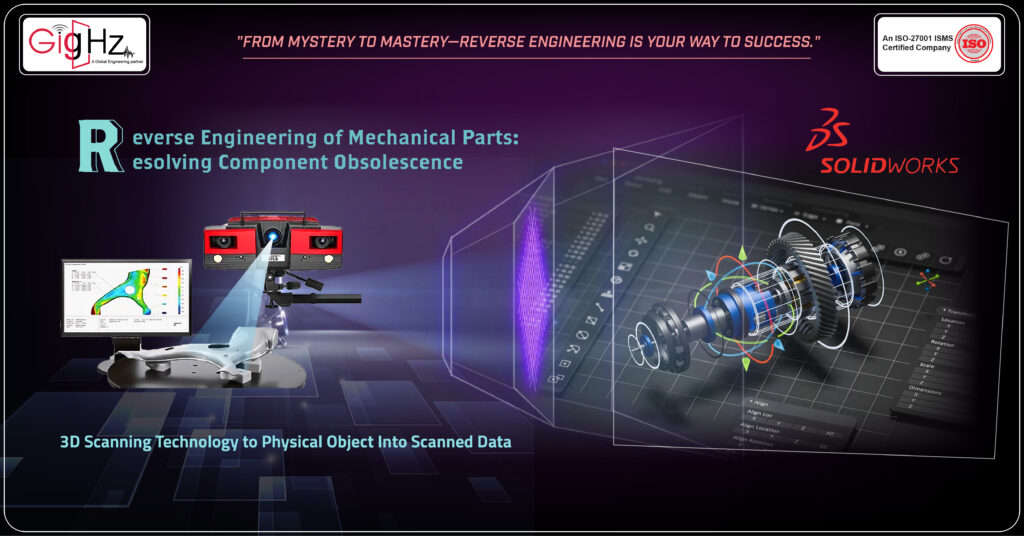
Book a Free Consultation Call​
Partner with Gighz and bring your most innovative design concepts to life. Our engineering cad services accelerate development so you can focus on your big vision.